3D-Druck-Simulation: Zeit und Kosten sparen bei der Motorenentwicklung
Anbieter zum Thema
Turin ist berühmt für seine beeindruckende, einzigartige Architektur und seine historische Bedeutsamkeit. Doch die Stadt hat mehr zu bieten, als hübsche Bauten und eine glanzvolle Geschichte. Nahe dem Stadtkern befinden sich die Fertigungshallen von Punch Torino. Das Unternehmen hat sich auf die Entwicklung von Verbrennungsmotoren und Antriebssystemen spezialisiert. Eine Simulations-Software von Markforged unterstützt Punch Torino jetzt bei der Entwicklung der Motoren.
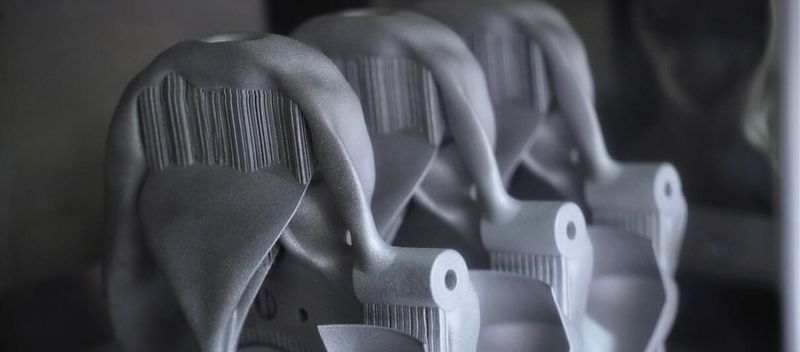
3D-Druck-Simulation in der Praxis: In Turin baut das Unternehmen eine Reihe von Motorprototypen für seine Kunden und entwickelt und testet neue Komponenten für existierende Motormodelle. Während des Bauprozesses müssen die Ingenieure eine Steuerkette montieren, die die Kurbelwelle des Motors mit zwei Nockenwellen verbindet. Beim Drehen öffnen und schließen die Nocken entlang ihrer Länge die Ventile jeden Zylinders, um Kraftstoff und Luft zum korrekten Zeitpunkt hineinzulassen.
Das richtige Werkzeug durch 3D-Druck-Simulation
Beim Spannen des Steuerkettenrads müssen die Nockenwellen in einer definierten Position vollständig stillstehen, um eine perfekte Synchronisierung des Steuerungssystems bei laufendem Motor zu gewährleisten. Passiert das nicht und die Ventile öffnen und schließen sich zum falschen Zeitpunkt, kann das den Motor beschädigen oder gar zerstören.
Um das zu verhindern, haben die Ingenieure ein gabelartiges Verriegelungswerkzeug für die Nockenwelle aus Onyx mit Endlosfaserverstärkung entwickelt. Während des Spannens müssen die Werkzeuge einem Drehmoment von bis zu 120 Nm standhalten und dürfen keine Drehung zulassen. Das Werkzeug im 3D-Drucker zu drucken dauert ungefähr 18 Stunden.
Verzögerungen von bis zu einem Tag
Für den Bau von Motoren muss das Team von Punch Torino eine große Anzahl von Komponenten und Werkzeugen an einem Ort vorrätig haben, damit sie acht bis zehn davon innerhalb eines begrenzten Zeitfensters zusammenbauen können. Ein schlecht konfiguriertes Werkzeug kann unter Druck brechen. Wenn ein Verriegelungswerkzeug während des kritischen Spannprozesses bricht, führt das auf die Nockenwelle wirkende Drehmoment dazu, dass sie sich aus der Position dreht.
In einem solchen Fall muss die Steuerkette gelöst oder entfernt, die Nockenwellen erneut befestigt und der Spannvorgang neu gestartet werden. Oft bedeutet das, dass die Ingenieure warten müssen, bis das neue Verriegelungswerkzeug gedruckt ist. Das kann eine Verzögerung von einem Tag oder mehr bedeuten, vor allem dann, wenn dabei ein Zeitfenster für den Bau eines neuen Motors verpasst wird.
Während der Entwicklung eines Motors nehmen die Ingenieure außerdem viele kleine Konstruktionsänderungen an Motorkomponenten vor, insbesondere in den frühen Entwicklungsphasen. Das Team muss dann das Design des Verriegelungswerkzeugs für die Nockenwellen überarbeiten und neu drucken. Häufig testen die Ingenieure mehrere Designs für Nockenwellen gleichzeitig. Für jede Nockenwelle ist dabei auch ein etwas anderes Werkzeugdesign erforderlich.
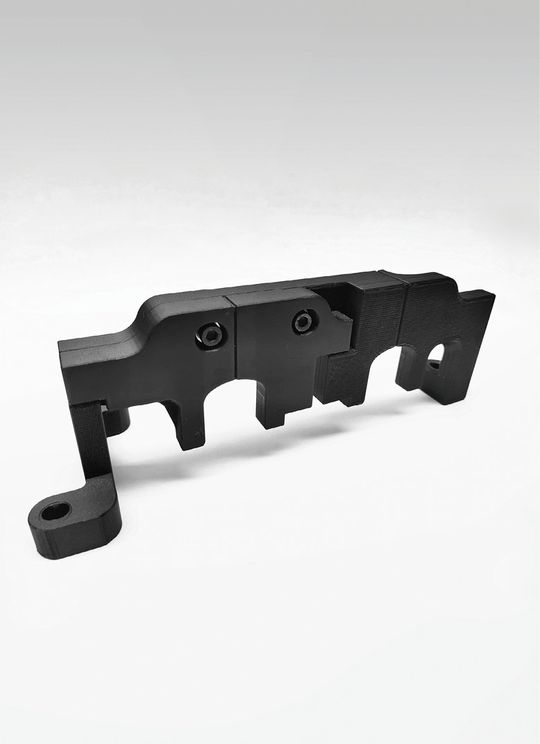
Der lange Weg zur korrekten Konfiguration
In der Vergangenheit war der Entwicklungsprozess des Verriegelungswerkzeugs für die Nockenwelle mit vielen Versuchen und Fehlern verbunden. Es gab keine genaue Methode, um vorherzusagen, ob ein Werkzeug steif und stark genug sein würde, um dem Drehmoment, mit dem es belastet wird, standzuhalten. Es war beinahe unmöglich, zu wissen, ob sich eine Änderung des Designs des Verriegelungswerkzeugs auf dessen strukturelle Integrität auswirken würde.
Da die Finite Element Analyse nicht auf Teile aus dem 3D-Druck ausgelegt ist, musste das Team viele Annahmen und Annäherungen machen, um Vorrichtungen zu entwerfen, die alle Anforderungen erfüllen. Für eine neue Konfiguration einer Nockenwelle bis zu acht Vorrichtungen entworfen, gedruckt und getestet werden, um die korrekte Konfiguration zu erzielen. Eine Aufgabe, die häufig mehrere Wochen in Anspruch nahm.
3D-Druck-Simulation statt endlos drucken
Mithilfe der Software für 3D-Druck-Simulation von Markforged sollten diese Testschleifen reduziert werden. Die Idee dahinter? Prototypen-Drucke und besonders solche Werkzeuge, wie in diesem Fall, nur noch einmal drucken zu müssen. Im System werden alle bekannten Daten, Lasten, Festigkeitsbedarf und weiteres eingetragen. Je nach Wunsch kann das Werkzeug dann virtuell angepasst werden. Entweder weil es fester sein soll, damit es nicht bricht oder damit der Druck schneller geht oder auch um Materialkosten einzusparen.
Nachdem die Arbeit mit der Simulation von Markforged begonnen hatte, konnte die Anzahl der durchschnittlichen Wiederholungen des Verriegelungswerkzeugs zumindest zu Beginn von acht auf drei verringert werden. Beim Erlernen des neuen Simulationswerkzeugs mussten einige Versuche und Fehler durchlaufen werden, bis die Grenzbedingungen, die Kraftmenge und die Verformung, denen das Verriegelungswerkzeug ausgesetzt war, korrekt festgelegt werden konnte. Da diese Daten nun erfasst sind, kann ein normales Verriegelungswerkzeug in der Regel in einer einzigen Iteration simuliert und gedruckt werden.
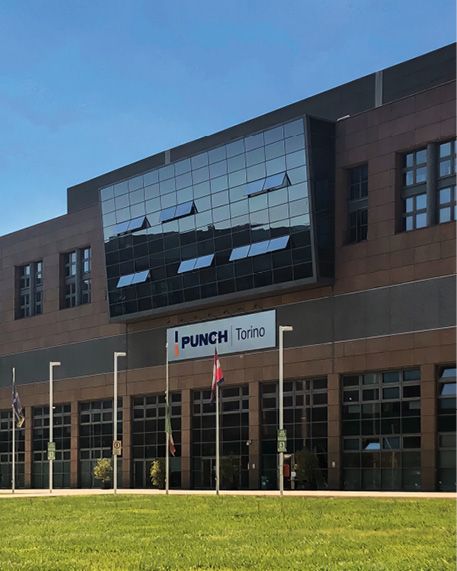
Dank 3D-Druck-Simulation 18 Stunden pro Vorrichtung gespart
In der Praxis sieht es so aus, dass zuerst ein Teil in der 3D-Druck-Simulation validiert und die Software dann genutzt wird, um die Druckeinstellungen und die Position der Carbonfaser zu optimieren. Dabei experimentiert das Team häufig mit verschiedenen Konfigurationen mit manuell platzierter Faser und vergleicht dann die geschätzte Durchbiegung und den Sicherheitsfaktor jeder Konfiguration. Mit der Simulation erkennen die Ingenieure in wenigen Minuten, wie die verschiedenen Faseranordnungen sich auf die Leistung des Teils auswirken. So kann schnell und einfach die leistungsfähigste Konfiguration für den Druck gefunden werden.
In den ersten Phasen der Motorentwicklung führen Ingenieure häufig Änderungen am Design der Nockenwelle durch. Wenn es sich um kleinere Änderungen handelt, ändert das Team das Design des Verriegelungswerkzeugs für die Nockenwelle und behält dabei den vorherigen Anwendungsfall in der Simulation von Markforged bei, um zu überprüfen, ob das Werkzeug noch immer die erforderliche Festigkeit aufweist. Wenn Entwicklungsingenieure größere Änderungen am Design der Nockenwelle vornehmen, muss das Team das Verriegelungswerkzeug neu entwerfen und die Simulation basierend auf dem neuen Design erneut durchführen.
Im Durchschnitt konnte das Team in etwa 18 Stunden pro Vorrichtung einsparen und die Entwicklungszeit für die Änderung der Teilekonstruktionen ist ebenfalls verkürzt, da dies auch in der Software ausgeführt wird. Darüber hinaus verringert sich die Belegung des Druckers erheblich, der zuvor für die zahlreichen Iterationen das Verriegelungswerkzeug verwendet wurde. So spart Punch Torino nicht nur viel Zeit, sondern stellt auch bessere Teile her.
Die Autorin Gesa Schneider ist Senior Territory Manager Central Europe bei Markforged.
Lesen Sie auch: Nvidia Omniverse: Schnelle Entwicklung autonomer Fahrzeuge mit Ansys