3D-Metalldruck: Der schnelle Weg zum optimalen Prototypen
Anbieter zum Thema
Bei der Entwicklung eines neuen Fahrrads gilt die Prototyping-Phase als besonders kritisch. In ihr werden wichtige Eigenschaften des Fahrrads wie Geometrie, Komfort und Stützkraft getestet, bevor endgültige Anpassungen für die Produktion vorgenommen werden. Da dies mit einem Kunststoffrahmen nur bedingt möglich ist, entschied man bei Kalkhoff, den Weg zum Metall-3D-Druck einzuschlagen.
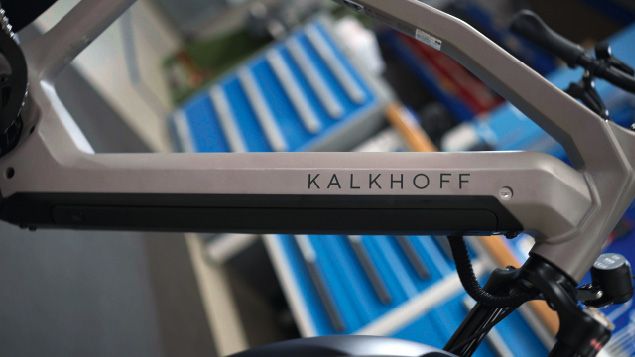
3D-Metalldruck im Praxistest: Kalkhoff ist ein deutscher Fahrradhersteller mit mehr als 100 Jahren Erfahrung in der Fahrradindustrie. Dank seiner langjährigen und bewegten Geschichte weiß das Unternehmen, worauf es bei der Herstellung eines guten Fahrrads ankommt. Dennoch ist die Produktentwicklung für ein neues Fahrrad immer ein Balanceakt. Insbesondere müssen die Designer die Geometrie des E-Bikes beibehalten und gleichzeitig die in das Design integrierten zusätzlichen Teile und Anbauten berücksichtigen.
3D-Metalldruck für den Rad-Prototypen
Daher testet das Unternehmen die Räder eines jeden Fahrrads über die üblichen Anforderungen der Branche hinaus. Normalerweise müssen Räder einer Belastung von bis zu 150 Kilogramm standhalten – einige Hersteller verzichten jedoch auf solche Tests. Im Vergleich mit anderen halten die Räder von Kalkhoff rund 170 Kilogramm aus. „Unser Unternehmen ist stolz darauf, seinen Kunden die Möglichkeit der Freiheit und Unabhängigkeit beim Radfahren zu bieten“, sagt Rik Maes, Industriedesigner der Kalkhoff Derby Cycle Werke. „Radfahren soll unser Firmenmotto widerspiegeln: ‚Kalkhoff moves you everywhere.“ Um dieses Niveau aufrechtzuerhalten, stützt sich das Unternehmen auf strenge Tests, die während der Prototyping-Phase durchgeführt werden. Kalkhoff braucht fahrbare Modelle, an denen Standard- und Sonderteile montiert und überprüft werden können, um das Design zu perfektionieren. Die Prototypen müssen also genauso aussehen und sich genauso anfühlen wie das endgültige Fahrrad. Da dies mit Kunststoffrahmen nur schwer zu erreichen ist, suchte das Unternehmen nach anderen Möglichkeiten. Vor allem interessierte es sich für den Metall-3D-Druck.
Umstieg von Kunststoff auf Metall
Kalkhoff hatte Materialise Manufacturing bereits zuvor für gedruckte Kunststoffprototypen genutzt und war von dem Service und der Qualität beeindruckt. Vor kurzem wurde das Team von Kalkhoff jedoch auf einer Messe auf die Möglichkeiten des 3D-Drucks von Aluminium, den Materialise im Portfolio hat, aufmerksam und entschied sich, diesen Weg für seine neuen E-Bikes weiter zu verfolgen. „Kalkhoff ist ein uns bereits sehr vertrauter Kunde, was die Sache vereinfachte. Da unser neues Metall-Kompetenzzentrum für 3D-Druck in Bremen zudem in der Nähe des Kalkhoff-Hauptsitzes in Cloppenburg liegt, schien es offensichtlich, die Geschäftsbeziehung für dieses Projekt fortzusetzen“, sagt Philip Buchholz, Innovation Manager Metall-3D-Druck bei Materialise.
Zunächst erstellte das Design- und Ingenieurteam von Kalkhoff die 3D-Modelle und wandelte sie in eine druckbare Datei um. Das Team arbeitete dann mit Materialise zusammen, um die Entwürfe zu optimieren und die vorteilhaftesten Merkmale auszuwählen, bevor das Modell gedruckt wurde. Schließlich wurde der mehrteilige Rahmen von einer speziellen Kette von Zulieferern und Experten für additive Fertigung (AM) geschweißt, wärmebehandelt und gerichtet. „Kalkhoff profitierte bei der Umstellung von Kunststoff auf Metall von unserem Know-how und unserem hochmodernen 3D-Fertigungsnetzwerk, in dem über 30 Materialien verarbeitet werden“, erklärt Philip.
Mehrere Schritte liefen parallel
„Da der zur Verfügung stehende Platz für Metall-3D-Drucker ziemlich begrenzt ist, musste der Rahmen in mehreren Segmenten fertiggestellt werden“, erklärt Philip weiter. „Nach dem Druck wurde der Rahmen bei unserem zuverlässigen Partner, der Seefried GmbH in Bremen, geschweißt und getestet. ACTech kümmerte sich um die Wärmebehandlung des geschweißten Rahmens, die in zwei Schritten – Lösungsglühen und Warmauslagern – durchgeführt wurde», fährt er fort.
Bestimmte Schritte wurden parallel durchgeführt, um den Prozess noch weiter zu optimieren. „Während des 3D-Drucks der einzelnen Komponenten wurden gleichzeitig das Konstruktionsschweißen und die Wärmebehandlung des Rahmens anhand der CAD-Daten des Fahrradrahmens durchgeführt“, erklärt Michael Röhner, Produktmanager für 3D-Metalldruck bei ACTech. „Situationen wie diese und Momente wie die nach der Glühphase (die Echtzeitmessungen des Rahmens mit millimetergenauer Geometrie erfordern) sind ohne enge Zusammenarbeit und das Fachwissen aller Beteiligten nicht möglich“, sagt er.
Aufgrund der Bauweise des Fahrrads waren Faktoren wie Geschwindigkeit, Kommunikation und der Standort bei der Herstellung der Metall-Prototypen von entscheidender Bedeutung. „Die Kommunikation mit dem Team von Materialise war offen, transparent und schnell – was bei der Konstruktion der Prototypen äußerst hilfreich war. Wir haben die gleiche Denkweise und Auffassung von Qualität“, sagt Rik. „Außerdem konnten wir durch die Produktion unserer Rahmen mit ihren lokalen Partnern Zeit sparen und schneller testen, ohne uns um lange Transportwege kümmern zu müssen.“
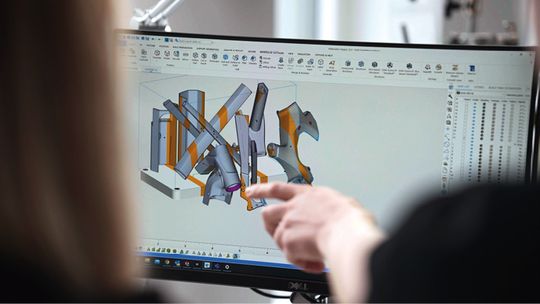
Dank 3D-Metalldruck: Funktionsfähiger Prototyp in nur sechs Wochen
Normalerweise dauert die komplette Entwicklung eines Fahrrads zwischen 2 und 2,5 Jahren. Durch den Einsatz von Metall-3D-Druck und AM-Experten in diesem Bereich konnte jedoch in der letzten Entwicklungsphase viel Zeit eingespart werden. „Wir haben es geschafft, den gesamten Rahmen innerhalb von sechs Wochen zu liefern“, sagt Philip. „Mit diesem neuen Prozess werden in der Entwicklungsphase etwa drei Monate eingespart“, fügt Rik hinzu.
Für Kalkhoff ist die Fertigungsqualität von entscheidender Bedeutung. Beim 3D-gedruckten Prototyp aus Metall gelang es dem Fertigungsteam, die Schnitte am Fahrrad unter Berücksichtigung der vorhandenen Belastungen neu zu positionieren, um Spannungsspitzen an den Schweißnähten zu vermeiden.
Das gesamte Team war begeistert vom 3D-gedruckten Prototypen aus Metall und freute sich, diesen testen zu können. Außerdem ist der Aluminiumrahmen ein voll funktionsfähiger Prototyp – ein deutlicher Vorteil gegenüber den Kunststoffvarianten, die hauptsächlich zu Werbezwecken dienen. „Wir haben gelernt, dass es sich sehr gut mit einem 3D-gedruckten Aluminiumrahmen fahren lässt“, sagt Rik. Der Materialwechsel ermöglichte es dem Team von Kalkhoff, realistische und genaue Funktionstests durchzuführen und die Montage von Anbauteilen zu prüfen. „Der Motorflansch und das Lager der Gabel sind besonders wichtige Schnittstellen, die auf Funktionalität und Sicherheit geprüft werden müssen“, sagt Philip.
„Das Fahrrad hat einen unserer dynamischsten Belastungstests mit 170 kg ohne Probleme bestanden. Das hat uns ein wenig überrascht; wir sind vom technischen Standpunkt aus sehr beeindruckt“, fährt Rik fort.
Für Probefahrten geeignet
Neben den Funktionstests ist der Metall-Prototyp auch für Veranstaltungen geeignet. Kunden können das Fahrrad auf Messen Probe fahren und so die Marke vor der Markteinführung kennen lernen. Rik betont, dass solche Demonstrationen für das Markenbewusstsein und die Verdeutlichung der Vorteile des 3D-Drucks im Allgemeinen von großer Bedeutung sind. „AM eignet sich hervorragend für unsere Tests und Veranstaltungen. Zum Beispiel ist unsere Ausstellung Kalkhoff Brand World ein hervorragender Ort, um solche Prototypen zu präsentieren. Außerdem eröffnet sich eine großartige Möglichkeit, in Zukunft produktiver und nachhaltiger zu produzieren, da beim 3D-Metalldruck weniger Material verloren geht.
Der Autor Frank Küchelmann ist Marketing Manager bei der Materialise GmbH in Bremen.
Lesen Sie auch: Carbon-Leichtbau-Feldhäcksler bringt Nachhaltigkeit in die Landwirtschaft