Getriebeauslegung: Durch Simulation zum optimalen Ergebnis
Anbieter zum Thema
Seit 2007 schrauben und tüfteln die Mitglieder des Kaiserslautern Racing Teams (KaRaT) an Rennwagen und stellen sich mit ihren Boliden im internationalen Konstruktionswettbewerb Formula Student regelmäßig der Konkurrenz. Seit der Saison 2011/12 ist das Team auch mit einem Elektrowagen dabei. Derzeit dreht sich alles um den neuen Rennwagen für 2023: Der „Electronyte e23“ beinhaltet erstmals seit 2020 wieder größere Innovationen.
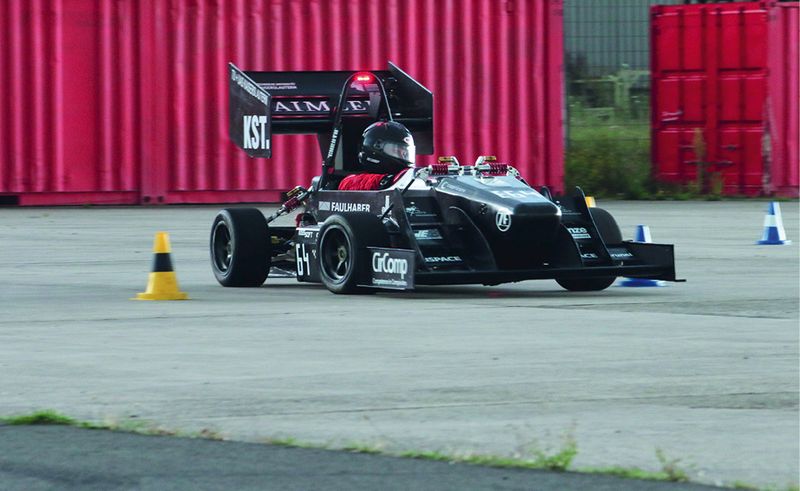
Jedes Jahr baut das studentische Rennsportteam für den Wettbewerb Formula Student einen neuen Wagen, der den Vorgaben und Regularien entsprechen muss. Das Reglement lässt den jungen Studierenden jedoch viele Freiheiten und gibt ihnen die Möglichkeit, ihre eigenen Ideen einzubringen und schlussendlich umzusetzen. Viel Arbeit für die interdisziplinäre Crew, die sich aus etwa 30 bis 40 Studierenden von der RPTU und der Hochschule Kaiserslautern zusammen setzt. Das Projekt wird vollständig von den studentischen Mitgliedern verwaltet und organisiert. Dies umfasst nicht nur die Leitung der verschiedenen Gruppen wie Chassis, Fahrwerk, Antriebsstrang, Getriebeauslegung und Elektronik, sondern auch Marketing, Planung und Beschaffung.
Autonomes Fahren weiterentwickelt
Die bereits seit 2020 entwickelten Funktionen des autonomen Fahrens sollen beim neuen Rennwagen erstmals nahtlos in das elektrische System integriert werden und in ausgewählten Disziplinen fortan den Fahrer komplett ersetzen. Spezielle Sensoren und Recheneinheiten erkennen die durch Pylonen abgesteckte Strecke und ermöglichen die Berechnung der Ideallinie. Der Aufbau des 600-V-Hochspannungsakkus wird für das neue Auto stark überarbeitet, was zu einer kleineren und leichteren Lösung führen wird. Kombiniert wird dieses Konzept mit einem selbstentwickelten Battery Management System (BMS), welches direkt auf die zugekauften Hochleistungs-Li-Ionen Batteriezellen aufgeschraubt wird. Ziel des BMS ist, neben dem Schutz der Zellen, auch die genaue Berechnung der verbleibenden Akku-Kapazität, um diese maximal auszunutzen und die verfügbare Energie optimal im Auto verteilen zu können. Alle Komponenten werden in einem neu konzipierten Carbon-Monocoque untergebracht, welches gleichzeitig den Fahrer schützt
Herausforderung Monocoque
Die Konstruktion des Monocoque stellt eine große Herausforderung dar und erfordert den ständigen Austausch unter den Teammitgliedern. Bauräume für Akku, Fahrwerk und Antrieb müssen klar abgestimmt sein. In einem iterativen Prozess, in dem viele Kompromisse eingegangen werden, entsteht so das Gesamtkonzept des Rennwagens. Das Monocoque muss den Sicherheitsanforderungen des Reglements entsprechen. Die Konstrukteure müssen durch zahlreiche Tests und Berechnungen der CFK-Strukturen nachweisen, dass das Monocoque den Fahrer im Falle eines Unfalls ausreichend schützt.
Die Fertigung des Monocoque fordert die Unterstützung des gesamten Teams. Es investiert rund 500 Stunden, um das finale Monocoque zu erhalten. Man beginnt mit dem Kleben einer groben Chassi Form aus Ureol-Blöcken, einem speziellen Kunststoff. Aus dieser Form wird dann mittels einer großen CNC-Fräse eine Positivform des Monocoque gefräst. Die Oberfläche der Positivform ist identisch zu der finalen Oberfläche des Monocoque. Genauer sind es mehrere Formen, in die die Form aufgeteilt ist. Diese werden nun aufwendig vorbereitet, geschliffen und chemisch bearbeitet, bevor sie mit Carbon überzogen werden. Das Team stellt sich so seine Negativform her. Diese entspricht auf ihrer Innenseite der Oberfläche des finalen Monocoque. Das Ureol wird nun mit einer fünf- bis sieben Millimeter dicken Carbonschicht versehen und in einem Autoklav ausgebacken. Die Negativformen lassen sich nun von der Kunststoffform trennen. Auch die Negativform wird nun geschliffen und chemisch bearbeitet bevor die nächsten Schritte folgen.
Die Formen können nun an dafür vorgesehenen Punkten verschraubt werden. Ihre Innenseiten bilden zusammen die Außenhaut des finalen Monocoques ab. Dies ermöglicht das Laminieren des Monocoques im Inneren dieser Negativform. Die Form wird als finaler Schritt wieder auseinandergeschraubt und ermöglicht so das Entformen, das Lösen des Monocoque aus der Form. Doch zuvor legt das Team Lage für Lage Carbon aufeinander, um die gewünschten mechanischen Eigenschaften zu erzielen. Organisiert wird sich hierbei im Schichtbetrieb rund um die Uhr.
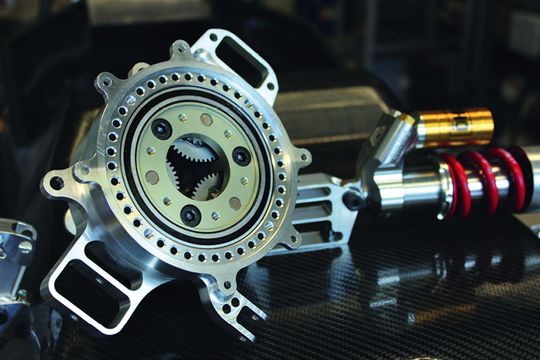
Getriebeauslegung mit Kisssoft
In der Saison 2020/2021 ist dem Team der Umstieg von einem heckgetriebenen Auto auf ein Allrad-Konzept mit Radnabenmotoren gelungen, wodurch in dem 200 kg leichten Gefährt die gesamte Kraft der 80 kW (110 PS) Systemleistung auf die Rennstrecke gebracht werden kann. Um die 20.000 Umdrehungen pro Minute der Motoren auf eine nutzbare Drehzahl zu reduzieren und das Drehmoment an den Rädern zu maximieren ist ein eineinhalbstufiges Planentengetriebe verbaut. Durch die Auslegung des verwendeten Getriebes mit Kisssoft konnte jenes so klein und kompakt ausfallen wie möglich. Im Jahr 2022 wurde das gleiche Getriebekonzept mit Detailverbesserungen weitergenutzt. Durch das Radnaben-Packaging in diesem Konzept mussten jedoch Abstriche bei der Lenkung aufgrund von Kollisionen mit der Lenkstange gemacht werden. Grund hierfür war ein weit aus der Radnabe herausstehender Motor. Dieser bewegt sich an der gelenkten Vorderachse mit dem Rad mit und fordert so einen großen Bauraum ein, welchen das Team mit einer aufwändigen Mehrkörpersimulation untersucht hat.
Getriebe mit neuem Wirkprinzip
Für die kommende Saison wird nun ein Getriebe mit einem anderen Wirkprinzip konstruiert: Statt den Planetenträger als abtreibendes Element zu nutzen, wird das Rad nun über das Hohlrad angetrieben. Dadurch wird der axiale Bauraum des Getriebes deutlich kleiner. Die daraus resultierende Vergrößerung des Getriebedurchmessers, stellt mit einem selbstgefertigten Felgenstern kein Problem mehr dar. Der neu entstandene Freiraum ermöglicht dem Fahrwerksteam eine bessere Auslegung der Lenkkinematik und erhöht die Wendigkeit des Rennwagens, wovon sich das Team ein angenehmeres Fahrgefühl für den Piloten und damit verbundene Verbesserungen der Rundenzeiten erhofft. Die Software von Kisssoft ermöglichte es dem Antriebsteam, in der kurzen Entwicklungszeit diese Konzeptänderung vorzunehmen. Besonders die intuitive Optimierung des Getriebes mit Kisssoft gefiel den Entwicklern. Die realistische Darstellung der Zahnräder in der Kisssoft-Umgebung ermöglichte es dem Team früh eine Vorstellung zu bekommen, wie solch ein Getriebe später aussehen wird.
Getriebeauslegung first: Erst die Arbeit, dann das Rennen
Nun liegt es am Kaiserslautern Racing Team die Entwicklungen umzusetzen. Nach der Fertigung der Teile steht der Zusammenbau der Komponenten sowie die Getriebeauslegung an, gefolgt von Tests auf Prüfständen. Erst dann können die Testfahrten durchgeführt werden. Sie stellen die letzte Hürde für die Neuentwicklungen und das ganze Auto dar. Die Belohnung erhält das Team dann im Sommer auf den Events in ganz Europa.
Autor: Presseabteilung des Kaiserslautern Racing Teams.
Lesen Sie auch: Getriebe: Diese Kupplung zeigt Ihnen die Zähne