Energieeffiziente Antriebstechnik Energieeffiziente Antriebstechnik: Auf das Gesamtsystem kommt es an
Anbieter zum Thema
Insbesondere Servomotoren sind schon heute sehr energieeffizient. Doch nomineller und tatsächlicher Wirkungsgrad liegen oft noch weit auseinander. Mit einer systemischen Perspektive lässt sich hier ein großes Einsparpotenzial aufdecken.
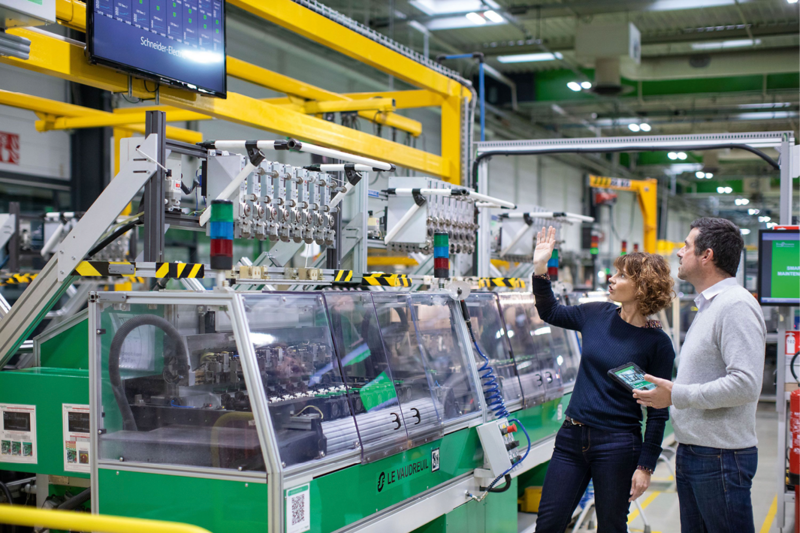
Energieeffiziente Antriebstechnik unter der Lupe: Beim Thema Energieeffizienz geht es längst nicht mehr nur um Klimaschutz. Ein sparsamer, das heißt nachhaltiger Umgang mit Energie, ist für den Großteil der deutschen Industrie zu einer geschäftskritischen Frage geworden. Für nahezu sämtliche Branchen stellen die zuletzt stark gestiegenen Strompreise eine enorme Belastung dar. Laut einer Umfrage der DIHK im Herbst 2022 planen daher schon mehr als 50 Prozent der deutschen Industrieunternehmen die Implementierung von Energieeffizienztechnologien. Neben der Nachrüstung von bestehenden Anlagen kommt es dabei insbesondere auf die Konstruktion von energieeffizienteren Maschinen an – insbesondere die Antriebstechnik nimmt dabei eine Schlüsselrolle ein.
Günstige Gelegenheit für den Maschinenbau: Energieeffiziente Antriebstechnik
Schon 2020 war beim VDMA in Sachen nachhaltiger Technologien von einer günstigen Gelegenheit die Rede. In einer gemeinsam mit Boston Consulting Group durchgeführten Studie hieß es, dass die Bereitstellung von nachhaltiger und energieeffizienzsteigernder Ausrüstung „Umsatzmöglichkeiten von 10 Billionen Euro bis 2050“ bieten könne. Und noch eine weitere optimistische Botschaft hielt die Studie parat: Denn allein mit der Implementierung von bereits verfügbaren und wirtschaftlich rentablen Technologien sei es möglich, die weltweiten CO2-Emissionen der größten Industriesektoren um rund 37 Prozent zu senken. Ein zentraler Ansatzpunkt dabei: elektrische Motoren.
Der Systemgedanke ist entscheidend
Wie das Umweltbundesamt errechnet hat, entfallen auf elektrische Antriebe und die mit ihnen betriebenen Funktionen rund zwei Fünftel des gesamten deutschen Stromverbrauchs. Logisch also, dass viel Geld eingespart werden könnte, wenn der Bedarf an dieser Stelle sinkt. Aber wie so oft, braucht es eine differenziertere Sicht. Denn Tatsache ist auch: Stand heute sind die allermeisten elektrischen Antriebe, insbesondere wenn es sich um Servomotoren handelt, schon enorm energieeffizient. Während es selbst die effizientesten Verbrennungsmotoren kaum auf 50 Prozent schaffen, verfügt ein handelsüblicher IE3-Motor mit 75 kW Leistung über einen Wirkungsgrad von gut 96 Prozent. Daran lässt sich kaum noch optimieren.
Aber, und dazu kann erneut die bereits erwähnte VDMA-Studie zitiert werden, „auch die effizientesten Motoren können ihr Potenzial nicht vollständig nutzen, wenn sie nicht auf den jeweiligen Anwendungszweck abgestimmt werden.“ Heißt: neben der Mikrosicht auf Einzelkomponenten – etwa den drehzahlvariablen Antrieb – ist vor allem die systemische Makroperspektive für die Optimierung der Energiebilanz eines Antriebssystems entscheidend. Denn gerade in Anwendungsfällen, bei denen viele verschiedene Antriebe miteinander kombiniert werden müssen, zum Beispiel in Verpackungsmaschinen, ist es auch mit energieeffizienten Antrieben keine Selbstverständlichkeit, ein wirklich energieeffizientes Gesamtsystem zu betreiben.
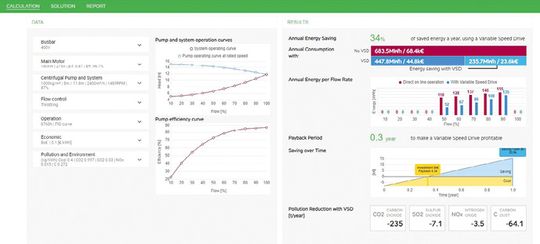
Energieeffiziente Antriebstechnik: Zwischenkreiskopplung sorgt für Ausgleich
Eine Möglichkeit, um ein aus vielen, für sich genommen schon sehr energieeffizienten Antrieben bestehendes Antriebssystem noch energieeffizienter zu gestalten, ist die Zwischenkreiskopplung. Dabei wird ein zusätzlicher Stromkreis zwischen den verschiedenen Antrieben etabliert, über den eine Art Ausgleich von überschüssiger und benötigter Energie realisierbar ist. Bei überschüssiger Energie handelt es sich zum Beispiel um Bremsenergie oder um Energie, die im Fall einer Hebeanwendung beim Herablassen einer Last entsteht. Damit diese, innerhalb des Gesamtsystems, erzeugte Energie nicht verloren geht, kann sie in einem Zwischenkreis gespeichert und sobald nötig wieder in Bewegungsenergie umgewandelt werden. Bei gleicher mechanischer Leistung wird also insgesamt weniger Energie aus dem Stromnetz bezogen.
Besonders effizient funktioniert ein Antriebssystem dann, wenn über eine Zwischenkreiskopplung Servo- und Asynchronmotoren zusammenarbeiten können. Da Asynchronmotoren meist kontinuierliche Prozesse (beispielsweise Förderbänder) betreiben, steht mit ihnen immer ein dankbarer Abnehmer für zwischengespeicherte Bremsenergie bereit. Auf diese Weise kann dann also insbesondere die Energieeffizienz von Asynchronmotoren nochmal um ein Vielfaches gesteigert werden.
Der Wirkungsgrad ist Auslegungssache
Dass es bei der Energieeffizienz-Betrachtung weniger auf den einzelnen Antrieb, als vielmehr auf das ganze Antriebssystem ankommt, macht sich auch bei der Auslegung einer Anlage bemerkbar. Denn der tatsächliche Wirkungsgrad eines Motors ist immer auch von dessen Beschleunigungsprofil sowie dem Betriebszustand abhängig. Da ein Elektromotor mit sinkender Auslastung in der Regel deutlich ineffizienter wird, ist schon bei der Planung einer Anlage auf die optimale Ausnutzung und das optimale Beschleunigungsprofil jedes einzelnen Antriebs zu achten. Überdimensionierungen – wie sie im Fall der mechanischen und elektrischen Auslegung meist gängige Praxis sind – sind in Sachen Wirkungsgrad absolut kontraproduktiv. Um dieser Anforderung auch bei der Orchestrierung komplexer Anwendungsfälle gerecht werden zu können, macht es Sinn, auf Softwareunterstützung zurückzugreifen.
Mit elaborierten Digital Twin Anwendungen ist es heute etwa schon möglich, den Energiebedarf einer elektrisch betriebenen Mechanik zu jedem Moment der Bewegung zu berechnen. Übertragen auf das komplette Antriebssystem können so an jedem Punkt einer Anlage, die am besten geeigneten Antriebe ausgewählt und innerhalb der Software schon vor der Konstruktionsphase auf ihren tatsächlichen Wirkungsgrad hin überprüft werden. Und übrigens: Ein Digital Twin ist nicht nur für Planung und Simulation von Wert. Läuft das ideale, virtuelle Abbild einer Anlage auch parallel zum realen Betrieb mit, lassen sich Wirkungsgradeeinbußen der Antriebe, die etwa durch mechanische Abnutzung von Motor oder physikalischen Bauteilen entstehen, relativ schnell erkennen und beheben.
Der Autor Reinholt Schlechter ist OEM Segment Manager bei Schneider Electric DACH.
Lesen Sie auch: Micro-Zahnräder für präzise Anwendungen in kleinen Bauräumen