3D-Pelletdrucker für Gussformen lässt die Herstellungskosten schmelzen
Anbieter zum Thema
Der Thermoformer Duo Form druckt große Tiefziehformen in 3D und nutzt dafür die Polymer-Pelletextrusion. Durch Kombination des 3D-Pelletdruckers EXT 1270 Titan und glasgefüllter Polycarbonatpellets konnte das Unternehmen Kosten und Vorlaufzeiten deutlich reduzieren und in Folge viele Aufträge gewinnen.
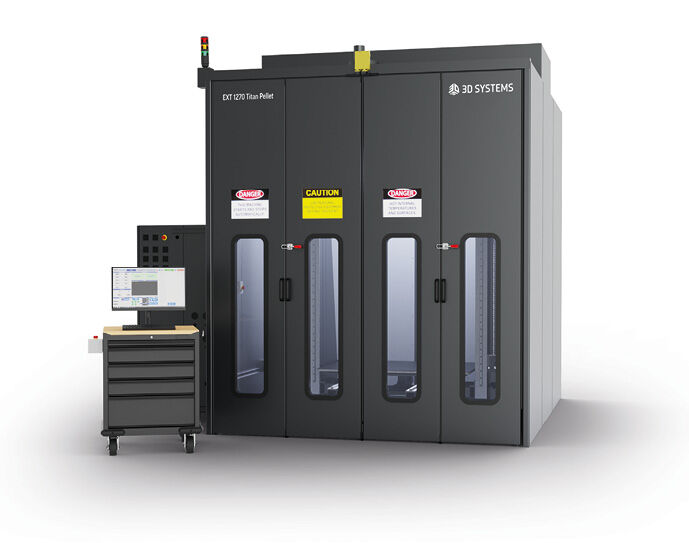
3D-Pelletdrucker in der Praxis: Um dem wachsenden Druck in der Lieferkette entgegenzuwirken, wenden sich Hersteller der additiven Fertigung zu, um schneller qualitativ hochwertige und kosteneffiziente Produkte herzustellen. Auch Unternehmen für Kunststoff-Thermoformverfahren haben herausgefunden, wie sie den großformatigen 3D-Druck mit Pelletextrusion und kostengünstigen Kunststoffpellets nutzen können, um sich einen Wettbewerbsvorteil zu verschaffen. Sie fertigen mittlere bis große Thermoformen in weniger als der Hälfte der Zeit und zu einem Bruchteil der Kosten im Vergleich zu herkömmlichen Methoden zur Formenherstellung. Doch wie können diese Unternehmen die additive Fertigung nutzen, um herkömmliche Vakuum- und Thermoformprozesse zu unterstützen und diese schneller, kosteneffizienter und agiler zu machen?
Subtraktiv vs. additiv gefertigte Formen
Beim herkömmlichen Thermoformprozess wird Kunststoffplattenmaterial in oder über Formen gezogen, um das fertige Teil herzustellen. Dieses Tiefziehen oder Thermoformen umfasst häufig auch Vakuumformen, wobei das Vakuum dabei hilft, die Kunststofffolie über die Form zu ziehen, um alle Details abzubilden. Formen für das Thermoformen können auf verschiedene Weise hergestellt werden, zum Beispiel durch Verwendung von Keramik und CNC-Bearbeitung von Metallen, Holz, Modellbauplatten oder durch manuelle Bildhauerei von Holz. Bei diesen subtraktiven Verfahren wird mit einer Spindel selektiv Material von einem Block entfernt, um die gewünschte Form für ein Muster oder eine Gussform zu erzeugen.
Im Gegensatz dazu bauen additive Fertigungsverfahren ein Teil Schicht für Schicht auf. Mit additiven Prozessen können Teile aus einer breiten Palette von Polymeren hergestellt werden, darunter Standard- und Hochleistungsthermoplaste, duroplastische, gefüllte und photopolymere Harze und sogar Metalle. Die Herstellung von Formen mithilfe der additiven Fertigung ermöglicht eine Gestaltungsfreiheit, die mit herkömmlichen Methoden nicht erreichbar ist. Für die Produktion muss nur genau die Menge an Material – im Allgemeinen ein Polymer – verwendet werden, die zur Herstellung des Teils erforderlich ist. Hierdurch werden Abfall und Kosten reduziert. Schließlich werden die Durchlaufzeiten für die Lieferung einer Form oder eines Urmodells durch die additive Fertigung erheblich reduziert – von Wochen und Monaten, die bei der herkömmlichen Fertigung erforderlich sind, auf Stunden oder Tage.
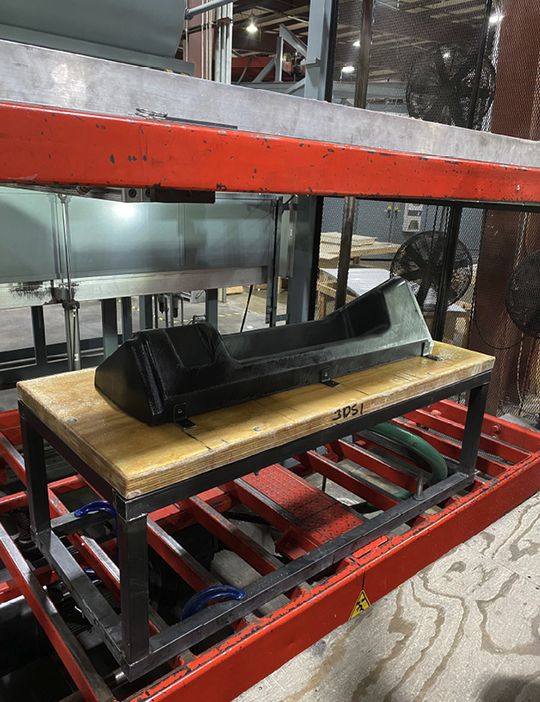
3D-Pelletdrucker: Großformatiger Druck mit Pelletextrusion
Beim 3D-Druck von Produktionsformen für Thermoform- und Vakuumformverfahren ist es wichtig zu überlegen, welche 3D-Drucktechnik für die herzustellende Form geeignet ist. Die Pelletextrusion eignet sich am besten für mittelgroße bis große Teile mit einer Größe von bis zu etwa 1 x 1,5 Meter. Für noch größere Teile können mehrteilige Formen erstellt und zu einer größeren endgültigen Produktionsform zusammengesetzt werden. Daher setzen Vakuum- und Thermoformunternehmen auf die 3D-Drucktechnologie mit Pelletextrusion, um die Vorlaufzeiten zu verkürzen, die Kosten für die Formenherstellung zu senken und die Flexibilität der Produktion zu erhöhen.
Der Direktdruck mit Thermoplastgranulat bietet mehrere Vorteile, insbesondere dann, wenn es um die Verringerung der Teilekosten geht. Thermoplastpellets gelten als der kostengünstigste Rohstoff für die additive Fertigung. Diese kosten bis zu zehnmal weniger als andere Druckmaterialien, wie zum Beispiel thermoplastische Filamente. Über die Materialkosteneinsparungen hinaus bieten 3D-Pelletdrucker erhebliche Geschwindigkeitsvorteile, da sie Formen mit einer Größe von bis zu 1270 x 1270 x 1820 Millimeter unter Verwendung von Hochleistungs- und Hochtemperaturmaterialien und mit Geschwindigkeiten von bis zu einem halben Meter pro Sekunde drucken können.
Auswahl des Pelletausgangsmaterials
Beim 3D-Druck von Produktionsformen für Thermoform- und Vakuumformprozesse ist es wichtig, den Formverzug zu minimieren, um ein qualitativ hochwertiges Endnutzungsteil zu erzielen. Thermo-formunternehmen haben für solche Anwendungen glasfaserverstärkte Polycarbonat-Pellets als bewährtes Material validiert, zusammen mit kohlenstofffasergefüllten ABS-Pellets und sogar einigen Polyamidpellet-Ausgangsmaterialien als brauchbare Formmaterialien.
Bei der Identifizierung und Auswahl eines Pelletausgangsmaterials für additiv gefertigte Formen sollten mehrere Faktoren berücksichtigt werden, wie die Stärke der endgültig geformten Folie und die Temperaturanforderungen des Endmaterials sowie die Verfügbarkeit und die Kosten des Pelletausgangsmaterials. Wenn beispielsweise eine Platte mit geringerer Stärke als die fertig geformte Platte verwendet wird, sind Formenmaterialien für niedrigere Temperaturen akzeptabel, wie beispielsweise CF-ABS-Pellets. Für Anwendungen, die eine größere Stärke erfordern oder ein Plattenmaterial mit höheren Temperaturspezifikationen, sollten auch für den Druck der Form Pelletrohstoffe für höhere Temperaturen verwendet werden, wie z. B. GF-PC oder gefülltes Polyamidmaterial.
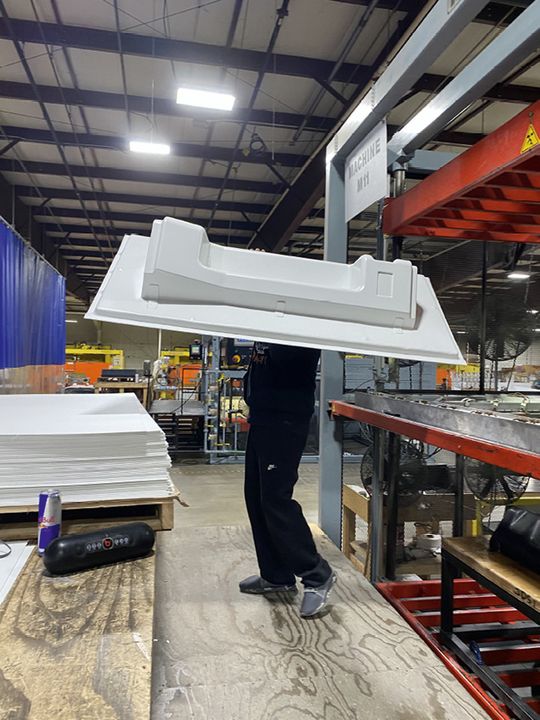
Vakuumlöcher ohne Werkzeuge dank 3D-Pelletdrucker
Ein weiterer Vorteil der additiven Fertigung bei der Herstellung von Tiefziehformen ist die Möglichkeit, eine poröse Oberfläche des gedruckten Teils zu nutzen, durch die ein Vakuum in die Form eingebracht werden kann, ohne dass spezielle Werkzeuge zum Herstellen der Vakuumlöcher verwendet werden müssen (wie es bei der herkömmlichen Methode der Fall ist). Anwender berichten, dass die inhärente Porosität von 3D-gedruckten Formen ein wesentlicher Vorteil der Verwendung der 3D-Pelletdrucker im Herstellungsprozess der Formen ist. Je nach gewünschtem thermogeformten Endnutzungsteil kann es notwendig sein, den Vakuumfluss durch die Form zu bestimmten Zonen, wie z. B. tiefen Hohlräumen, zu priorisieren, um sicherzustellen, dass der Formprozess das Teil wie erforderlich hervorbringt. Dies kann durch Anpassen der Werkzeugwegparameter vor dem Drucken erreicht werden. Das Drucken mit höherer Auflösung führt zu einer besseren Oberflächenbeschaffenheit, und die Anforderungen werden durch die Ausgangsdicke des geformten Materials bestimmt.
Innovationen schnell umsetzen
Auf dem wettbewerbsintensiven Markt für thermogeformte Kunststoffe arbeitet Duo Form, ein in Michigan ansässiger Marktführer im Bereich Thermoformen, für eine Vielzahl von Branchen kontinuierlich daran, seinen Herstellungsprozess zu erneuern, Durchlaufzeiten zu verkürzen und Kosten zu senken, um seine Kunden besser bedienen und neue Kontrakte gewinnen zu können. Gleichzeitig ist es für das Unternehmen entscheidend, die Qualität und Langlebigkeit der Formen beizubehalten. Zeit- und Kostenersparnis sind nicht die einzigen Herausforderungen, denen sich das Unternehmen stellen muss. Es muss außerdem Innovationen schnell durch Designiterationen und die Fertigung von Prototypen in Originalgröße umsetzen, um Verzögerungen im Genehmigungs- und Produktionsprozess zu vermeiden.
Form für Zuginnenverkleidung im 3D-Druck
Nachdem Duo Form sich für die additive Fertigung für die Produktion von Formen für großformatige Teile entschieden hatte, nahm das Unternehmen ein Projekt in Angriff, bei dem eine 1294 x 410 x 287 Millimeter große Zuginnenverkleidung in 3D gedruckt wurde. Das Projekt bewies, dass eine Kostensenkung von bis zu 88 Prozent und eine Reduzierung der Vorlaufzeit von 65 Prozent im Vergleich zu herkömmlichen Methoden mit Keramikformen möglich ist. Das Verfahren zeigte noch größere Einsparungen im Vergleich zu herkömmlichen Aluminiumformverfahren.
Duo Form arbeitete mit 3D Systems zusammen, um die additive Fertigung in seinen Herstellungsprozess zu integrieren und durch den 3D-Druck von Produktionsformen, Werkzeugen und repräsentativen Modellen für Thermoformen und Vakuumformen agiler zu werden. Durch die Kombination des 3D-Pelletdruckers EXT 1270 Titan (ehemals Titan Atlas 3.6) und glasgefüllter Polycarbonatpellets senkt Duo Form die Kosten drastisch und verkürzt die Vorlaufzeiten. Mit seiner ersten 3D-gedruckten Form, einer Duschwanne für Freizeitfahrzeuge, erzielte Duo Form sofortige Ergebnisse. Die additiv gefertigte Form erwies sich als hochwertig und hatte eine ähnliche Langlebigkeit wie herkömmlich hergestellte Formen. Tatsächlich wurden mehr als 1.000 Exemplare ohne nennenswerten Verschleiß aus der Form gezogen.
„Wir haben mit unserem Titan 3D-Drucker viele Aufträge gewonnen“, so David Rheinheimer, Produktentwicklungsmanager bei Duo Form. „Die Durchlaufzeit für Teile, Formen und Formteile hat uns einen enormen Vorsprung gegenüber unserer Konkurrenz verschafft.“ Seit der Implementierung der additiven Fertigung in seinen Fertigungsprozess hat das Unternehmen mehr Aufträge gewonnen. Dank der Geschwindigkeit und Agilität der 3D-Pelletdrucker können Verträge schneller abgeschlossen werden. Als Beispiel erwähnt Rheinheimer ein Modell, das Duo Form in 3D druckte, um es einem Kunden zusammen mit einem Angebot zum Formen des Teils zu präsentieren. Der Kunde war beeindruckt von der Geschwindigkeit und der Möglichkeit, das endgültige Design vorab zu sehen, und erteilte Duo Form noch am selben Tag den Zuschlag. Dies ist für Duo Form heute Standard und bringt seinen Kunden einen Mehrwert.
3D-Pelletdrucker ist Vorreiter
Die additive Fertigung verändert die Dynamik, wie Unternehmen über Produktionsprozesse denken. Der großformatige 3D-Druck mit Pelletextrusion gehört zu den Technologien, die hier Vorreiter sind. Durch die Einführung dieser fortschrittlichen Technologie profitieren Branchenführer von einer höheren Geschwindigkeit, einem verbesserten Kostenmanagement und einer qualitativ hochwertigeren Teileproduktion. Während sich die Entwicklung von Innovationen fortsetzt, wird die additive Fertigung weiterhin ihre Fähigkeit unter Beweis stellen, die Zukunft der Produktion zu gestalten.
Der Autor Clay Guillory ist Director Titan bei 3D Systems.
Lesen Sie auch: 1zu1 investiert rund 1,5 Millionen Euro in 3D-Druck