Mikrofertigung: Was 3D-Drucker heute bereits können
Anbieter zum Thema
Im 3D-Druck geht der Trend zur Fertigung von Serienteilen. Wer prüfen will, ob sich ein kleinformatiges Bauteil dafür eignet, muss viele Faktoren wie Material, Volumen, Kosten und Toleranzen berücksichtigen. Können 3D-Drucker die geforderte Genauigkeit überhaupt erreichen? Wie wirken sich die mechanischen Toleranzen verschiedener 3D-Drucksysteme auf die Gesamttoleranz von Bauteilen aus?
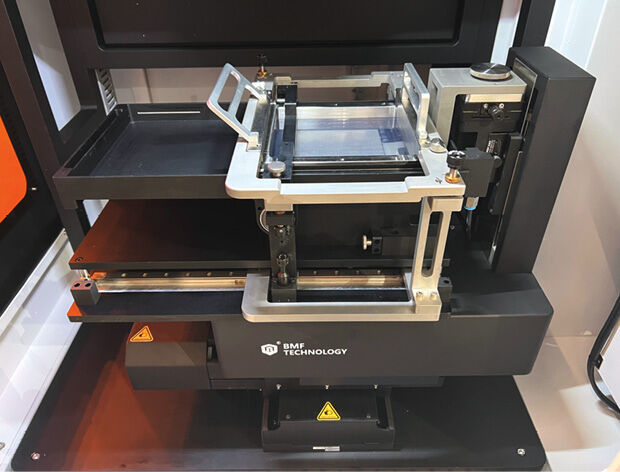
Viele Unternehmen nutzen den 3D-Druck bereits für die Mikrofertigung. Neue Verfahren ermöglichen hohe Designfreiheit und die Herstellung von Bauteilen, die sonst nicht machbar wären. Ob es gelingt, im 3D-Druck von Photopolymeren eine hohe Genauigkeit verbunden mit hoher Präzision zu erreichen, hängt von mehreren Faktoren ab. Die Auflösung der von Software gelieferten Daten spielt eine Rolle. Das Materialverhalten (Schrumpfung oder Ausdehnung) aber auch Materialabgabe und Schichtdicke spielen eine Rolle. Doch letztendlich werden alle diese Faktoren von der Toleranz des verwendeten Drucksystems begrenzt. Mit großzügigen Maschinentoleranzen lassen sich keine exakten Bauteilmaße erreichen. Genauigkeit und Präzision der Bauteile hängen damit von jeweiligen Verfahren und von den Druckertoleranzen ab.
Mikrofertigung: Mit Galvanometer und SLA-Drucker zur Präzision
Beim Standard SLA-Verfahren (Stereolithografie) tastet ein Laser die Oberfläche des Harzes ab, um die Schicht zu erzeugen. Der „Tisch“ bewegt sich nicht, nur der Laserpunkt. Um den Laser über die Oberfläche zu führen und das Harz auszuhärten, ist das System auf ein Galvanometersystem angewiesen. Die Maschinentoleranz wird durch die Qualität und Robustheit des Galvanometersystems bestimmt, das den Laser scannt, sowie durch die mechanische Bewegung des Tisches oder Lasers in Z-Höhe.
Galvanometer sind in der Regel eine gute Option für den Submillimeterbereich und eignen sich für eine Vielzahl von Anwendungen. Wenn es aber darum geht, eine Präzision und Genauigkeit im einstelligen Mikrometerbereich zu erreichen, genügen diese Systeme nicht. Kombiniert man die Maschinentoleranz von Galvanometern mit den höchstauflösenden SLA-Druckern auf dem Markt, die eine Laserpunktgröße von bis zu 25 μm erreichen, lassen sich in der Regel Maßtoleranzen von ± 100 μm erzielen.
Verzögerung der Masse beeinträchtigt Positioniergenauigkeit
Beim Material Jetting gibt ein Druckkopf Tröpfchen eines lichtempfindlichen Harzes ab, das sich unter UV-Licht verfestigt und das Teil Schicht für Schicht aufbaut. Die bei Material Jetting verwendeten Materialien sind duroplastische Photopolymere (Acrylate), die in flüssiger Form vorliegen. Querschnitte des Teils werden gedruckt und dann mit einer UV-Lichtquelle ausgehärtet.
Eine der Herausforderungen des Verfahrens bildet häufig ein Druckbalken oder Portal, das sich über die Bauoberfläche bewegt. Bei der Hin- und Herbewegung des relativ schweren Teils beeinträchtigen die Beschleunigung und Verzögerung der Masse die Positioniergenauigkeit. Bei diesen Systemen liegen die Maßtoleranzen in der Regel im Bereich von ± 300μm.
Gleichmäßige Energieverteilung als Herausforderung
Bei den meisten Standard-Digital Light Processing-Systemen (DLP) blendet ein Projektor das Bild des gesamten Querschnitts auf einmal ein, um eine Schicht auszuhärten. Dies bedeutet, dass Auflösung, Genauigkeit und Präzision von der Auflösung des Projektors, den optischen Eigenschaften des Projektionsobjektivs und der mechanische Z-Bewegung bestimmt werden. Die Fähigkeit, enge Toleranzen der Schichtdicke einzuhalten, hängt in hohem Maße von der Konstruktion des Z-Tisches ab.
Die zweite Herausforderung besteht darin, eine gleichmäßige Energieverteilung über den gesamten Bauquerschnitt zu erreichen. Sonst erhalten Features an den äußeren Rändern des Bettes weniger Energie als Merkmale in der Mitte des Bettes. Der gesamte Querschnitt des Teils wird auf einmal projiziert. Deshalb werden die Toleranzen von der Energiekonstanz des Projektorstrahls über die gesamte Fläche beeinflusst.
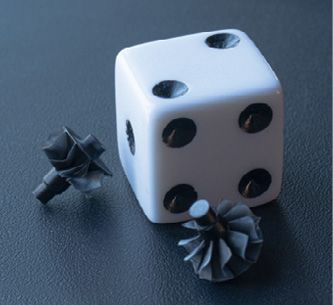
Projektionsmikro-Stereolithografie mit höherer Auflösung
Die Projektions-Mikro-Stereolithografie (PμSL) wurde von Boston Micro Fabrication (BMF) als Variante des DLP entwickelt, um deutliche höhere Auflösungen für Mikro- oder Präzisionsbauteile zu erreichen. PμSL verwendet dazu hochpräzise Optiken, welche die Pixelgröße im Projektor je nach System auf 25, 10 μm oder 2 μm fokussieren. Dank dieser leineren Pixelgröße verringert sich die Aufbaufläche, wodurch die Energie gleichmäßiger über die gesamte Projektionsfläche verteilt wird.
Das optische System muss diese Pixelgröße unbeeinträchtigt wiedergeben. Es wurde so ausgelegt, dass die Projektion weniger als 0,5 px Verzerrung aufweist, was bei den 2-μm-Systemen 1 μm entspricht. Es gewährleistet eine Gleichmäßigkeit der Lichtintensität von über 90 Prozent und ermöglicht damit eine äußerst präzise und genaue Projektion für die Mikrofertigung. So erreicht PµSL eine höhere Auflösung und kleinere Merkmale als andere Systeme.
Einhaltung enger Toleranzen in der Mikrofertigung
Doch die genauen Ergebnisse der Optiken müssen von hochpräzisen Lineartischen mit linearen Messgeräten umgesetzt werden. Durch diesen Aufbau bieten die mechanischen Bewegungen des gesamten Systems bidirektionale Positionswiederholbarkeit, Ebenheit und Geradheit, die Maschinentoleranzen liegen innerhalb von 3 μm. Dieser Ansatz funktioniert viel präziser, als Spindel- oder Riemenantriebe ohne lineare Messgeräte. Die mechanische Konstruktion des gesamten Systems, aber auch die Kalibrierung und Einstellung während der Montage, tragen ebenfalls zur Einhaltung enger Toleranzen bei. Auch während des Druckvorgangs sorgen Justier- und Positioniermechanismen der Drucker für die genaue Ausrichtung von Tischen und optischen Systemen und für präzise Anpassungen zwischen den einzelnen Druckvorgängen.
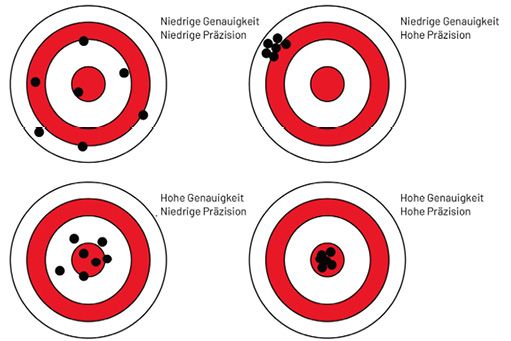
Genauer durch eingebaute Intelligenz
Schließlich enthalten Systeme von BMF einen Software-Algorithmus, der während des Druckvorgangs Toleranzüberlagerungen ausgleicht. Dadurch können auf der Druckplattform mehrere Zonen mit hoher Präzision und Genauigkeit zusammengefügt werden, wobei immer noch besonders kleine Features wiedergegeben werden. Dadurch können BMF-Drucker trotz geringer Pixelgröße auch größere Präzisionsbauteile herstellen.
Die 3D-Drucker von BMF kombinieren verschiedene High-end Technologien in einem System und erreichen damit hohe Genauigkeit, Präzision und Wiederholbarkeit. Viele der Konstruktionsmethoden für die Mikrofertigung wurden aus der Halbleiterindustrie übernommen, wo schon lange mit ähnlich geringe Toleranzen gearbeitet wird.
Kleine Pixelgrößen, höhere optische Genauigkeit und geringere Druckertoleranzen der 3D-Drucker von BMF führen direkt zu einer höheren Maßhaltigkeit und Wiederholungsgenauigkeit der Bauteile. Dies eröffnet neue Möglichkeiten der Serienproduktion in optimaler Qualität, etwa in der Mikrofluidik, der Medizintechnik, bei MEMS und in elektronischen Komponenten.
Die Autorin Laura Galloway ist Marketing Director bei Boston Micro Fabrication.
Lesen Sie auch: 3D-Drucksoftware 4D_Additive integriert 3D-Fertigungsformat