Digital Thread als Basis für erfolgreiches Product Lifecycle Management?
Anbieter zum Thema
In der Industrie 4.0 steht die Vernetzung von intelligenten Produkten und digitalisierten Prozessen im Vordergrund. Experten sprechen deshalb vom Digital Thread als Basis für erfolgreiches Product Lifecycle Management (PLM). Damit ändern sich das Konzept und die Umsetzung von PLM nachhaltig.
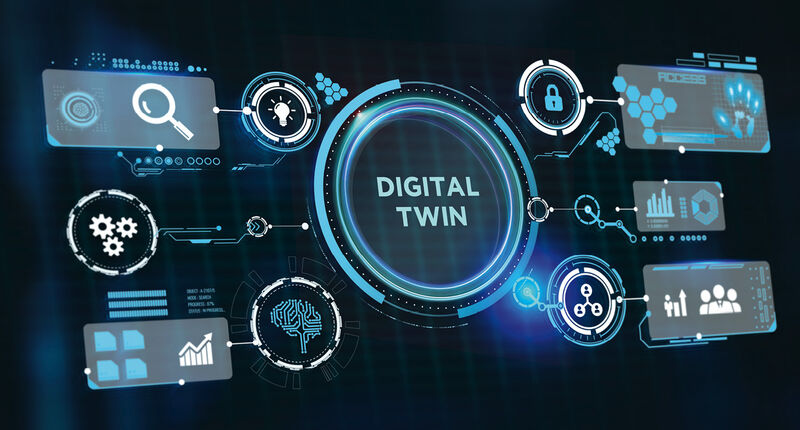
Digital Thread unter der Lupe: Neue Geschäftsmodelle wie Predictive Maintenance gehören zu den wichtigsten Anwendungen der Digitalisierung von Fertigungsprozessen und Produkten im Industriellen Internet der Dinge. Wenn beispielsweise die Wartung von Fahrzeugen nicht mehr starr an Zeiträume oder gefahrene Kilometer geknüpft ist, sondern an tatsächlichen Verschleiß, können alle Beteiligten Ressourcen sparen und gleichzeitig ungeplante Ausfallzeiten minimieren, also die Verfügbarkeit und den Nutzen erhöhen. Voraussetzung dafür ist allerdings, dass das Herstellerunternehmen über einen digitalen Zwilling des Produktes verfügt. Und hier scheitert traditionelles PLM.
Der Digital Thread für den Digital Twin
Das mag überraschen, da viele PLM-Hersteller seit langem mit dem Begriff des Digitalen Zwillings oder Digital Twin werben. Das Problem liegt in unterschiedlichen Deutungen des Begriffs Digital Twin. Zu unterscheiden ist zwischen einem Prozess-Zwilling, wie er seit Jahren – mehr oder weniger detailliert – in der Produktentwicklung zum Einsatz kommt und in einem PLM-System verwaltet wird und einem Produkt-Zwilling, der in den meisten Unternehmen noch eine Zukunftsvision darstellt. Denn der Produkt-Zwilling beruht auf einem Digital Thread, für den in der Regel die technischen Voraussetzungen nicht gegeben sind. Dazu später mehr.
PLM stößt schon beim Prozess-Zwilling an Grenzen
In PLM-Systemen bezeichnet der Digital Twin herkömmlicherweise einen Prozess-Zwilling. Seine Aufgabe ist es, technische Entscheidungen im Entwicklungsprozess nachvollziehbar zu machen. Hier geht es um Verfahren wie Visualisierung, Simulation und virtuelle Absicherung – bis hin zur virtuellen Inbetriebnahme. Außerdem unterstützt der Prozess-Zwilling die Planungsprozesse in der Produktion. Dazu erfordert der digitale Prozess-Zwilling ein durchgängiges Datenmodell mit sämtlichen relevanten Daten und Prozessinformationen. Kern des klassischen PLM sind in der Regel hoch komplexe Systeme. Sie vereinen Änderungs-, Dokumenten-, Produktstruktur-, Stücklisten-, Projektmanagement in einer Lösung. So sind sie grundsätzlich geeignet, sämtliche im Produktlebenszyklus benötigten Information abzubilden und zu verwalten, von der ersten Idee des Entwicklungsingenieurs bis hin zur Auslieferung des Produkts.
Dabei liegt die Betonung auf grundsätzlich geeignet. Nämlich dann, wenn tatsächlich alle Prozessergebnisse in dem System dokumentiert werden. Das ist jedoch in kaum einem Unternehmen der Fall. Tatsächlich habe ich selbst es in 20 Jahren als PLM Berater noch nie erlebt. Kein Wunder: In der Regel werden bei der Implementierung eines PLM-Systems nicht alle Altsysteme abgelöst, die benötigten Produktdaten werden über die Systemkette PLM-ERP-MES verwaltet oder die Komplexität des Systems ist so groß, dass die Anwender das System nicht mehr verstehen.
Damit alle notwendigen Produktprozesse im PLM-System abgebildet werden können, bedarf es komplexen System Customizings, das gerade aufgrund der Komplexität des Systems selten wirtschaftlich realisierbar ist – sonst wäre die Liste der PLM-Projekten mit nicht erreichten Zielen nicht so lang.
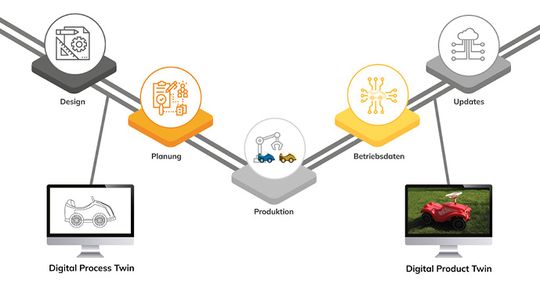
Produkt-Zwilling: Für das Produktleben nach der Auslieferung
In dieser Situation stehen die Fertigungsunternehmen heute vor der Herausforderung, eine andere Form von Digitalem Zwilling zu managen: Den Produkt-Zwilling. Dabei handelt es sich um die digitale Abbildung einer realen Instanz eines Produkts, eindeutig identifizierbar anhand einer Seriennummer. Im Unterschied zum Prozess-Zwilling sammelt der Produkt-Zwilling auch Informationen aus dem ERP- und MES-System und liefert Betriebs- und Simulationsdaten zurück. Daten, die beispielsweise zu einer nutzungsbasierten Abrechnung nach dem Prinzip Pay-per-Use dienen. Oder zum Angebot zusätzlicher Dienstleistungen, wie Over-the-Air-Updates von Softwarekomponenten in Maschinen oder Function-on-Demand. Auch automatische Anmeldungen von Wartungsarbeiten auf Basis der Nutzungsdaten im eingangs skizzierten Predictive Maintenance-Szenario sind möglich.
Darüber hinaus unterstützen Produkt-Zwillinge ein automatisiertes Kundenfeedback sowie maschinelles Lernen als Input für Neuentwicklungen, sowohl von Produkten als auch von zusätzlichen Serviceleistungen für individuelle Nutzungsszenarien. Dazu gehören etwa Empfehlungen bestimmter Lieferanten von Verbrauchsmaterialien wie Druckerpapier oder Maschinenöl auf Basis der Verschleißdaten, oder die automatisierte Order eines Ersatzteils und Wartungstermins beim Servicepartner, wenn Sensoren einen bestimmten Schwellenwert melden.
Herausforderung Digital Thread
Die Herausforderung des Digital Product Twin an das PLM ergibt sich dabei nicht allein aus der Verlängerung des PLM über die Grenzen des Auslieferungslagers hinaus. Die Probleme beginnen viel früher, nämlich bei der Verknüpfung aller zugehörigen Daten zu einem bestimmten Produkt in dem sogenannten Digital Thread. In einem klassischen PLM-System eines Automobilherstellers beispielsweise wäre es dazu erforderlich, dass sämtliche Zulieferer die Daten ihrer Teilprodukte, wie Materialmenge und -zusammensetzung, Abmessungen, Chargen, Prüfergebnisse in das PLM-System des Herstellers einspeisen.
Ein Verfahren, das spätestens dann unpraktikabel wird, wenn ein Zulieferer für verschiedene Hersteller mit unterschiedlichen PLMs arbeitet. Ganz abgesehen davon, dass schon unternehmensintern das PLM als einheitliche Plattform für alle Abteilungen eine Utopie darstellt, wie bereits erläutert. Genauso wie der Step-Standard zum Austausch von CAD- und Produktdaten bedarf es eines Standards zum Austausch von Daten zur Dokumentation eines digitalen Zwillings – ein interdisziplinäres Projekt zu diesem Thema wurde dieses Jahr bei ProStep iViP gestartet.
So sind denn auch Wissensgraphen und semantische Netzwerke die geeigneten Tools, um die Informationen aus den beteiligten Systemen zusammenzuführen. Anders als klassische PLM-Software verlangen sie nicht, sämtliche Daten in einer Datenbank zu lagern. Vielmehr verknüpfen sie die benötigten Informationen aus verschiedenen Anwendungen regelbasiert.
Der Autor Raul Radnai ist Senior Consultant bei der Abat AG.
Lesen Sie auch: SimAI beschleunigt Entwurfsprozess bei rechenintensiven Projekten