Digitaler Produktpass: Digitale Zwillinge für mehr Nachhaltigkeit im Engineering
Anbieter zum Thema
Spätestens im Jahr 2027 kommt die Pflicht zu Digitalen Produktpässen. Das Engineering steht damit vor der Aufgabe, Nachhaltigkeit noch einmal stärker als Teil der Produktentwicklung zu denken. Gerade im Maschinen- und Anlagenbau für die Prozessindustrie kann der Digitale Zwilling ein Ansatz für ein zentrales Datenmodell sein.
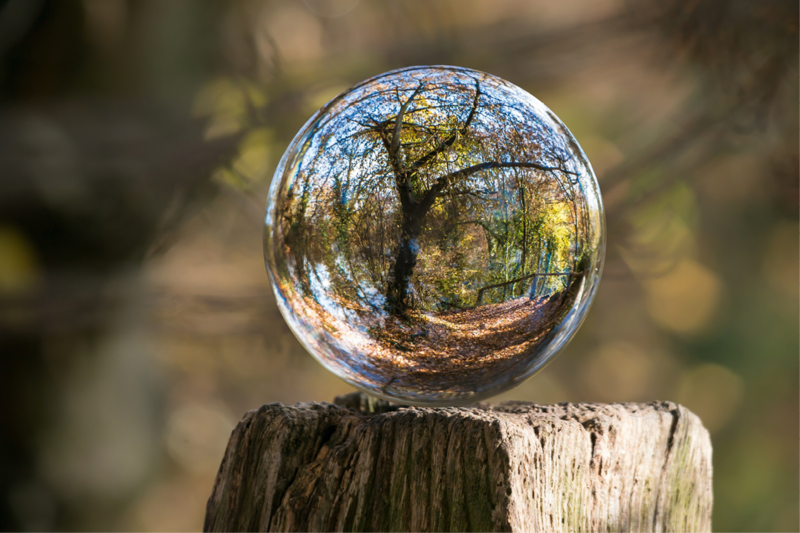
Digitaler Produktpass für die Umwelt: Obwohl das digitale Arbeiten im Engineering gang und gäbe ist, werden die dort erzeugten Daten oft noch nicht in der Wertschöpfungskette digital weitergegeben. Der Maschinen- und Anlagenbau wählt die Komponenten aus, plant die Produkte in 3D und stellt sie her. Schließlich entstehen auf dem Prüfstand und in der Inbetriebnahmephase weitere Daten, wenn die an den Kunden verkauften Parameter für die Gewährleistung überprüft werden. Doch bei der Übergabe an den Betreiber bleiben diese digitalen Daten bisher noch oft außen vor. Gerade in der Prozessindustrie bauen sich die Betreiber dann ihre eigene Informationswelt auf.
Green Deal: Digitaler Produktpass kommt
Die EU will mit dem Green Deal und der Öko-Designrichtlinie die Digitalisierung von Produkten und Kreislaufwirtschaft durch standardisierte Daten fördern. Mit dem digitalen Produktpass soll der Weg von einer linearen zu einer zirkulären Wirtschaft geebnet werden. Über den gesamten Produktlebenszyklus hinweg wird der digitale Produktpass künftig über standardisierte Schnittstellen mit maschinell lesbaren Daten befüllt. Ein digitaler Produktpass startet im Engineering des Produktes, reicht über dessen Herstellung in die Nutzungsphase und endet im Recycling. Das wird Auswirkungen auf das digitale Zusammenspiel aller Beteiligten in der Wertschöpfungskette haben. Hier kann das Modell des digitalen Zwillings als Verwaltungsschale von Eigenschaften der Objekte im Life Cycle einen technologischen Ansatz bieten.
Digitaler Produktpass: Plattform für Lebenszyklusdaten
Heute trägt vor allem die Herausforderung von mehr Nachhaltigkeit dazu bei, dass sich diese Herangehensweise ändern muss. Sinnvoller wäre es, wenn Maschinen- und Anlagenbauer das 3D-Modell übergeben, einschließlich der technischen Daten aus dem Engineering und der geprüften Auslegungsdaten. Schon jetzt werden einige Daten etwa an das Prozessleitsystem übertragen oder technische Zeichnungen und Dokumente weitergegeben. Allerdings fehlt insbesondere im Prozessanlagenbau und Maschinenbau meist eine Plattform, auf der alle Daten aus den unterschiedlichen Planungs- und Produktionssystemen sowie Service und Wartung zusammenkommen. Auch mit Blick auf den gesamten Lebenszyklus eines Produkts geht es darum, Informationen aus Produktentstehung, Betrieb, Wartung und Instandhaltung, Second Life und Recycling zu bündeln. Denn digitale Durchgängigkeit wird immer wesentlicher: Hier kann der Digitale Zwilling als Datenmodell – als Verwaltungsschale der Eigenschaften von Objekten – für die Weitergabe von Produktinformationen in einer digitalen Kette einen wichtigen Beitrag leisten. Dieser Digital Twin (DT) sollte künftig schon von der Entwicklungsabteilung der Maschinen- und Anlagenbauer ins Leben gerufen werden, die ganz am Anfang dieser Kette stehen.
Daten-Know-how wird entscheidend
Perspektivisch geht es um das Zusammenspiel unterschiedlichster Digitaler Zwillinge für Produkte, Anlagen und Prozesse. Grundlage ist die Verwaltungsschale (Asset Administration Shell für den Digitalen Zwilling) der Plattform Industrie 4.0. Mit dem Verein IDTA (Industrial Digital Twin Association) soll der interoperable Digitale Zwilling auch in mittelständischen Unternehmen etabliert werden. Dahinter stehen unter anderen die Verbände VDMA, ZVEI und der Bitkom. Die Verwaltungsschale bietet Planungssicherheit, wenn sich jetzt auch KMU mit der DT-Technologie befassen.
Wichtig ist natürlich auch, konzeptionell die passende Sensorik mitzuliefern, damit der DT in der Betriebsphase mit aktuellen IoT-Daten angereichert werden kann. Sie legen zugleich die Grundlage für Data Analytics rund um Energieoptimierung, Problemerkennung oder Predictive Maintenance. Für Konstrukteure und Ingenieure in der Entwicklung bedeutet das eine neue Herangehensweise und die intensive Auseinandersetzung mit den Daten.

Cloud-Plattform als zentrale Datendrehscheibe
Digitale Zwillinge basieren in der Regel auf Modellgrafen als Datenmodell. Als Grundlage bieten sich große Cloud-Plattformen an, die das automatisierte Kombinieren vieler unterschiedlicher Datenquellen ermöglichen. So stellt Microsoft Azure als Industrieplattform beispielsweise Cloud-Lösungen bereit, mit denen sich die Erstellung und Verwaltung von Digital Twins stark vereinfacht. Mit dem Azure Digital Twin ist der DT als Cloud-Service verfügbar und kann analog zur Verwaltungsschale genutzt werden. Die bereits erfassten Daten genügen damit den künftigen Anforderungen der Datenbereitstellung innerhalb einer Wertschöpfungskette.
Dieser Ansatz verbindet die Digital Twin Language, das Dataverse für das Handling der Daten und KI-Technologie wie ChatGPT. Mit der DT Definition Language lässt sich jedes beliebige physische Objekt beschreiben, etwa digitale Abbilder von Produkten, Ausrüstung, Anlagen, Maschinen oder Gebäuden. Wichtige Basisdaten für den Digitalen Zwilling wie die Auslegungsdaten aus Datenblättern und die Ergebnisse vom Prüfstand bei der Inbetriebnahme von Maschinen oder Anlagen können auch per App in digitale Modelle eingepflegt werden. Die so befüllten Modellgrafen ermöglichen die Erzeugung von verschiedenen Digitalen Zwillingen, sie sich wiederum für Simulationen kombinieren lassen – etwa um Energieverbräuche zu optimieren.
Ein Beispiel mit kritischem Blick auf energieintensive Ausrüstung
Viele Betreiber haben erkannt, dass sie angesichts hoher Energiekosten und neuer EU-Vorgaben bei der CO2-Einsparung die größten Verursacher in ihren Prozessen identifizieren müssen. Ganz weit oben auf der Agenda steht Rotating Equipment (wie etwa Pumpen und Ventilatoren), das jetzt perspektivisch einem Retrofit mit Sensorik unterzogen wird. So kommt zum Beispiel Steve Schofield vom Verband europäischer Pumpenhersteller Europumps zum Schluss, dass auf Pumpensysteme etwa ein Fünftel des weltweiten Strombedarfs entfällt. Damit sind innerhalb der EU die Pumpen in der Industrie der größte Einzelverbraucher. Sie stehen mit einem Stromverbrauch von über 300 Terawattstunden pro Jahr für über 65 Mio. Tonnen CO2-Emissionen. Ganz entscheidend ist dabei, dass die rotodynamischen Pumpen, die etwa 80 Prozent der installierten Basis ausmachen, in der Regel zwischen 20 und 30 Prozent überdimensioniert sind. Wäre es hier also nicht sinnvoll, gemeinsam mit den Ausrüstungsherstellern solch energieintensiver Ausrüstungen im Rahmen der Nachhaltigkeit und der CO2-Einsparung die digitale Kette zu schließen?
Auf einer gemeinsamen Plattform lassen sich über die Verwaltungsschale des Digital Twins zum einen die Auslegungs- und Prüfdatendaten des Herstellers und zum anderen die Betriebsdaten des Betreibers austauschen und so beide Seiten wertschöpfend unterstützen. Die neue Ausrüstung könnte beispielsweise schon bei der Auslieferung mit den nötigen Sensoren für ein Monitoring bestückt sein. Ein Energieeffizienz-Label – ähnlich wie es bereits bei der Wärmepumpe zum Einsatz kommt – stellt zugleich einen guten Ausgangspunkt für den digitalen Produktpass dar. Klar ist: In der Zusammenarbeit auf Basis einer gemeinsamen Digital-Twin-Plattform lassen sich die Daten für einen digitalen Produktpass im Sinne der Nachhaltigkeit künftig deutlich einfacher bereitstellen.
Der Autor Udo Ramin ist Director of Competence Center Industry 4.0 & IoT bei Cosmo Consult.
Lesen Sie auch: Nachhaltige Schutzelemente für die Elektromobilität