Fabriksimulation: 3D-Software für die perfekte Visualisierung
Anbieter zum Thema
Um den Marktanforderungen nach kundenindividueller Massenproduktion gerecht zu werden, beauftragte ein Hersteller von Badmöbeln das Unternehmen Toolcraft, eine Fertigungsanlage für „Losgröße 1“ zur automatisierten Montage von individuellen Schubkästen zu entwickeln. Toolcraft visualisierte die Anlage zunächst mit einer Fabriksimulationssoftware und machte damit gute Erfahrungen.
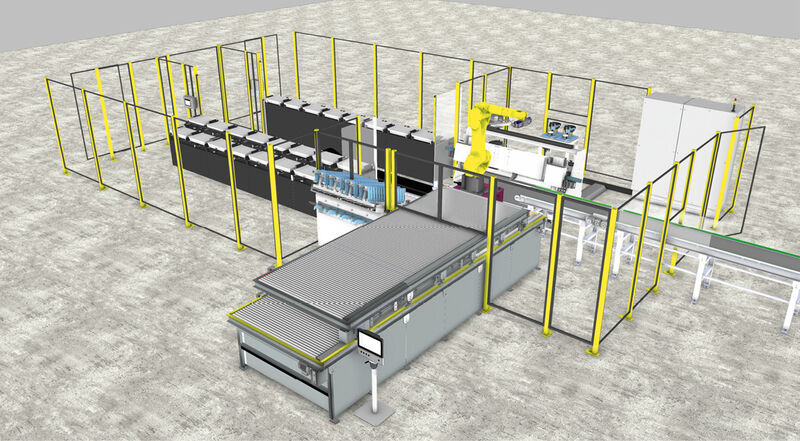
Fabriksimulation im Praxiseinsatz: Der Trend zu kundenindividueller Massenproduktion zeigt sich nicht nur in der Automobilindustrie, wo die Kunden schon lange zwischen zahllosen Extras bei der Konfiguration ihres neuen Fahrzeugs wählen können, sondern auch bei Möbeln. Das gilt ganz besonders für Badezimmermöbel, die oft in einem eng definierten Raum eingebaut werden müssen, und bei denen eine breite Palette an Maßen, Farben und Oberflächen gefordert ist. Als weitere Komplexität kommen hierbei noch die technischen Gegebenheiten eines jeden Badezimmers dazu, wie Anzahl, Form und Größe der Waschbecken, Dusch- und Badewannen und Anzahl und Bauart der Siphons.
Wie die Fabriksimulation bei Losgröße 1 helfen kann
Um den Wünschen des Kunden nach maßgeschneidertem Mobiliar gerecht zu werden, beauftragte ein bekannter Hersteller von Badmöbeln den Anlagenbauer Toolcraft, eine Roboteranlage zur automatisierten Montage von Schubkästen für seine Produkte zu entwickeln. Dabei sollten die Schubkästen mit beziehungsweise ohne Siphon verschiedenste Baugrößen aufweisen, von einem kleinsten Schub mit 170 Millimeter bis zum größten Schub von 1450 Milliemeter.
Der Möbelhersteller forderte außerdem eine Fertigung von verschiedensten Varianten mit individueller Material- und Farbauswahl mit „Losgröße 1“. Das heißt, jedes Möbelstück sollte bei Bedarf als Sonderanfertigung hergestellt werden können. Denn: Mit moderner Fertigungstechnik kann selbst Losgröße 1 für den Hersteller rentabel und für den Kunden erschwinglich sein.
Vor der Automatisierung wurde die Montage händisch mit Handwerkzeugen durchgeführt; die Zargen wurden mit dem Boden über eine pneumatische Presse verpresst. Die neue Anlage sollte eine Produktion im Zwei-Schichtbetrieb ermöglichen; sie sollte manuelle Prozesse erleichtern und monotone Tätigkeiten automatisieren.
Machbarkeitsstudie und Visualisierung
Nach der Anfrage des Kunden wurden in der Konzeptphase eine Machbarkeitsstudie und eine Visualisierung durchgeführt. Dafür verwendete Toolcraft die Fabriksimulationssoftware von Visual Components. Mit ihr lassen sich maßgeschneiderte Produktionssysteme entwerfen, simulieren, optimieren und validieren.
In der neu konzipierten Anlage werden nach dem Einlegen und der Zuführung der Holzbauteile die Bauteildaten über einen Scanner erfasst und verarbeitet. Mit einem Roboter werden die einzelnen Bauteile einer automatischen Montagestation zugeführt und dort verschraubt beziehungsweise verpresst. Anschließend werden die fertig montierten Schubkastensysteme mit dem Roboter auf ein Förderband gelegt und zu einer Station transportiert, wo sie von Hand entnommen und kommissioniert bzw. eingelagert werden.
Das Besondere an diesem Projekt: Es ist die erste Anlage für eine „Losgröße 1“-Fertigung in der Möbelherstellung. Die Planung und Umsetzung und der Bau der Anlage dauerten circa eineinviertel Jahre.
Bibliothek in der Fabriksimulation erleichtert die Planung
Eine der Herausforderungen bestand für Toolcraft darin, dass die Anlage eine komplexe Sensorik und Anlagenüberwachung erfordert, denn die Bauteile müssen präzise zueinander positioniert werden. Um die volle Flexibilität zu gewährleisten, war es erforderlich, das Handling aller Bauteilvarianten mit nur einem flexiblen Greifersystem zu realisieren. Außerdem musste eine vollautomatisierte Montagepresse entwickelt und in die Anlage integriert werden.
Ausgangspunkt bei der Planung einer solchen Anlage ist in der Regel ein 2D-Layout. Ausgehend von diesem Entwurf werden Fabrikkomponenten wie Förderanlage, Montagepresse, Roboter und Greifer zu einer Anlage zusammengestellt. Dabei konnte Toolcraft auf die von Visual Components mitgelieferte Bibliothek zugreifen; wenn eine spezielle Maschine nicht in der Bibliothek vorhanden war, konnte sie aus einem vorhandenen CAD-Modell erstellen und in die Bibliothek einfügen. Visual Components besitzt Schnittstellen zu allen wichtigen CAD-Systemen.
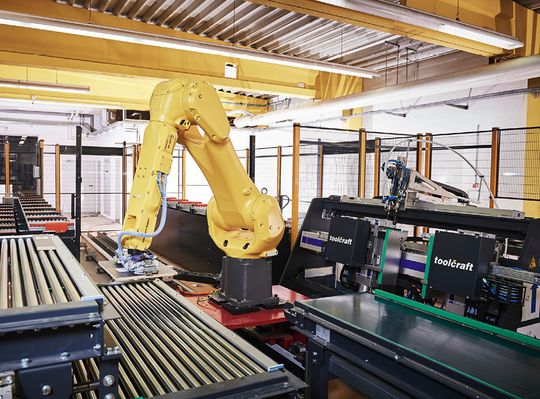
Machbarkeit sicherstellen am Modell
Die Lösungen von Visual Components haben bei der erfolgreichen Abwicklung des Projekts entscheidend geholfen. Zunächst wurde die gesamte Anlage virtuell aufgebaut und visualisiert. Anhand des virtuellen Modells wurde die prinzipielle Machbarkeit des vom Kunden gewünschten Konzepts sichergestellt.
In der Bibliothek sind die exakten Abmessungen der Fabrikkomponenten hinterlegt. So konnten am virtuellen Modell von Visual Components sehr einfach Tests zur Reichweite der Roboter und zur Erreichbarkeit sämtlicher Arbeitsbereiche durchgeführt werden. Das erleichterte die Platzierung der Montagepresse, des Roboters und der Förderanlagen.
In der Visual Components Bibliothek sind aber auch weitere wichtige Attribute hinterlegt. Zum Beispiel die Bewegungsparameter der Roboter, anhand derer auch exakte Zeit- und Bewegungssimulationen durchgeführt werden können. Mit ihnen ließ sich die Gesamtanlage optimieren, indem sie am Modell die minimal möglichen Taktzeiten ermittelten. So konnte man dem Kunden den wirtschaftlichen Nutzen der Anlage genau nachweisen.
Komplexe Anlagen durch Fabriksimulation veranschaulichen
Dank Visual Components konnte somit nicht nur die technische Machbarkeit ermittelt und der wirtschaftliche Nutzen quantifiziert werden. Das mit der Simulationssoftware erstellte Modell machte es für Toolcraft auch viel einfacher, die Anlage und den Ablauf der Fertigung beim Kunden zu präsentieren und zu veranschaulichen.
„Wir setzen die Lösungen von Visual Components in unserem Unternehmen bei allen Projekten ein, die eine Visualisierung und eine Machbarkeitsanalyse benötigen“, erklärt Bernd Krebs, Geschäftsführer bei Toolcraft. Besonders schätze man, dass die Prozessabläufe, selbst bei komplexen Anlagen, einfach visualisiert und auch „Nicht-Technikern“ veranschaulicht werden können. „Auch die Kalkulation und Preisfindung werden sehr vereinfacht, weil wir die gesamte Anlage vorher digital aufbauen können,“ so Krebs weiter. „Wir planen, Visual Components auch zur Simulation anderer Prozessabläufe in unseren weiteren Fertigungskompetenzen einzusetzen, beispielsweise bei der additiven Fertigung und der Zerspanung, im Formenbau und Kunststoffspritzguss sowie für die automatisierte Qualitätsprüfung.“
Im Ergebnis haben Toolcraft und Visual Components dem Badmöbelhersteller dabei geholfen, die Wünsche seiner Kunden nach individuellen und dennoch bezahlbaren Produkten zu erfüllen. Als erfreulichen Nebeneffekt kann man festhalten, dass der Durchsatz der Produktion bei gleichbleibender Qualität gesteigert werden konnte, und dass viele monotone Tätigkeiten jetzt vom Roboter übernommen werden – eine Win-Win-Situation für alle Beteiligten.
Der Autor Chris Douglass ist Geschäftsführer bei der Visual Components GmbH.
Lesen Sie auch: Effizienzsteigerung: Der digitale Zwilling optimiert den Kaffeegenuss