Digitalisierung Offline-Programmierung: Roboteranlagen effizient steuern
Anbieter zum Thema
Bei der Implementierung einer Software zur Offline-Programmierung von zwei Roboteranlagen mussten Auftraggeber Diehl Aviation und Software-Anbieter Cenit einige technologische und operative Herausforderungen meistern, die am Ende aber sowohl die Software als auch die Prozesse bei Diehl Aviation entscheidend voranbrachten.
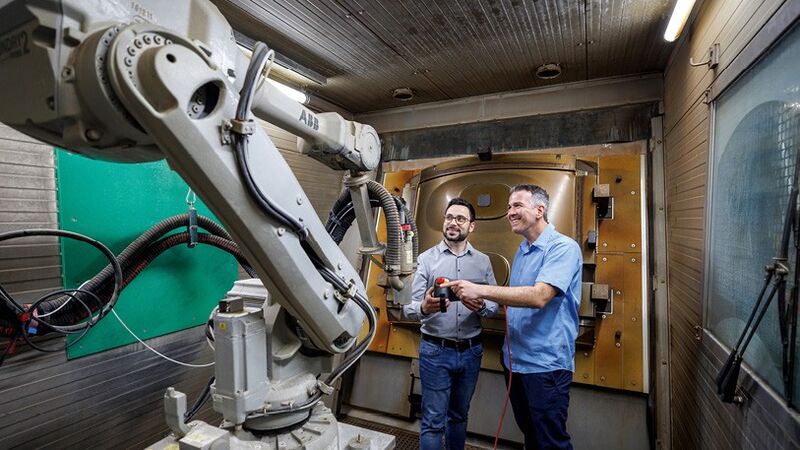
Wenn Passion für die Luftfahrt auf die Liebe zur Perfektion trifft.“ So beschreibt sich Diehl Aviation selbst. Auf den ersten Blick ungewöhnlich für ein hochtechnisiertes Unternehmen, das mit rund 4.400 Mitarbeitern und 889 Millionen Euro. Umsatz (2022) ein klarer Tier-1-Player der Luftfahrtindustrie ist.
Jedoch sind Passion und Perfektion wichtige Komponenten, um den eigenen Anspruch an die Leistungen, Produkte und Services zu erfüllen, die Diehl Aviation täglich bereitstellt: Als internationaler Zulieferer für Flugzeugsystem- und Kabinenlösungen stattet das Unternehmen weltweit nahezu alle namhaften Flugzeughersteller aus. Ob Avionik, Kabinenausstattung inklusive Bordküchen, Bordtoiletten, Sanitärlösungen für Flugzeuge Brandschutz, Wasserversorgung und Klimatisierungen sowie umfangreiche Retrofit-lösungen zählen zu Diehls Portfolio, das den gesamten Lebenszyklus des Flugzeugs umfasst.
Der digitale Faden über allem
Diehl Aviation investiert seit jeher kontinuierlich in die Weiterentwicklung seiner Technologien und Prozesse. Um Leistungen und Produkte effizienter und nachhaltiger herzustellen, soll sich ein „digitaler Faden“ durchgängig über die gesamte Wertschöpfungskette des Unternehmens ziehen. Daten, Informationen und Prozesse sollen bestmöglich digital verknüpft und nutzbar gemacht werden. Ergänzt wird der Ansatz durch die Zielsetzung einer größtmöglichen Automatisierung von Abläufen und Prozessen – da wo es technologisch und wirtschaftlich sinnvoll ist.
Gesucht: Lösung zur Offline-Programmierung für Roboteranlagen
Diese Maxime leitete nun auch ein Ende 2019 gestartetes Vorhaben: die Implementierung einer Software zur Offline-Programmierung von zwei Roboteranlagen: Einer 8-Achs-ABB-Roboteranlage für das Laser-Schweißen von Kunststoffteilen sowie einer Roboteranlage für die automatisierte Reinigung von Presswerkzeugen. Bei der letzteren sollten durch Offline-Programmierung rund 200 unterschiedliche Programme für die Oberflächenreinigung der jeweiligen Werkzeugsätze entstehen.
Diehls Anforderungen an die Lösung: Zum einen sollten beide Anlagen mit einer Software programmiert werden können. Zum anderen sollte eine Anbindung der Software an das zentrale SAP-System möglich und integraler Bestandteil der Lösung sein. „Bei Diehl Aviation war bekannt, dass Cenit eine eigene Software-Lösung für den Bereich Digitale Fabrik entwickelt hatte. Im Jahr 2019 kam man mit der Anfrage auf uns zu, ob wir mit unserer Software die jeweiligen Roboter-Anlagen programmieren könnten“, erklärt Dieter Konrad, Senior Account Manager bei Cenit.
„Die Offline-Programmierung ist eine der Kern-Stärken unserer Software, der Fastsuite E2 – und da war es klar, dass wir dies auch unter Beweis stellen wollten“, so Konrad weiter. Ein Demo-Termin vor Ort und ein anschließender Proof-of-Concept überzeugten den Luftfahrtzulieferer. Entscheidend war die Tatsache, dass Cenit nicht nur Diehls Ansprüche an die Offline-Programmierung der Roboter erfüllen, sondern auch die durchgängige Konnektivität der Fastusite-E2-Software zum SAP-System abdecken konnte.
Herausfordernder Auftakt
Nun wäre die Geschichte über die Implementierung einer Software zur Offline-Programmierung bei Diehl Aviation rasch erzählt, gäbe es nicht drei zentrale Herausforderungen, die den zeitlichen Ablauf des Projekts beeinflussten. Die aber letzten Endes alle beteiligten Partner in ihrem technologischen Agieren und auch in Bezug auf die Zusammenarbeit erheblich weitergebracht haben.
Die erste Herausforderung: „Wir besaßen noch kaum Erfahrung in Bezug auf hoch automatisierte Roboter-Systeme und deren Programmierung“, erinnert sich Daniel Kohn von Diehl Aviation. So war es beispielsweise auch nicht sofort möglich, die ursprünglichen Catia-Modelle der Fertigungsmittel oder der zu reinigenden Werkzeuge in Fastsuite zu laden, da die Aufbereitung der entsprechenden Datenmodelle nicht dem nötigen Standard entsprach. „Es erforderte Einiges an Entwicklungsarbeit seitens Cenit, dass wir diese Modelle nun nicht mehr auf unserer Seite bearbeiten müssen“, so Jürgen Böhringer, Key-User Tool Engineering bei Diehl Aviation.
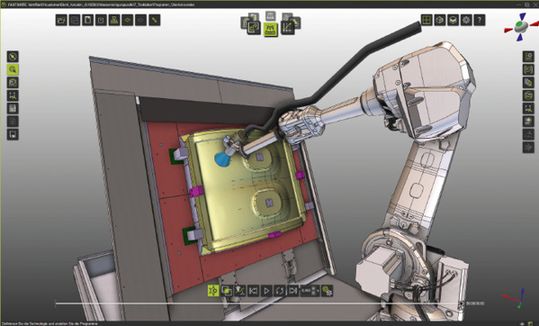
Die zweite Herausforderung: Der Oberflächen-Reinigungsprozess von Presswerkzeugen für die Luftfahrtindustrie ist komplex und birgt eigene Besonderheiten. Obwohl Cenits Fastsuite E2 zahlreiche branchenbezogene Spezifikationen in ihren Bibliotheken beinhaltet, war dieser spezielle Prozess technologisch noch nicht in der Software abgebildet. „Die notwendigen Funktionalitäten und Anforderungen kamen sukzessive zutage. Letztendlich mussten wir dann im laufenden Projekt das Technologie-Paket seitens der Softwareentwicklung her erweitern“, so Konrad. Softwareseitig, so Konrad weiter, war dies eine gut lösbare Aufgabe. Für Cenit bestand die Herausforderung allerdings darin, personelle Ressourcen in der Softwareentwicklung freizumachen, die für die Erweiterung des Technologie-Pakets notwendig waren. „Und ja, das hat den zeitlichen Horizont nach hinten verschoben,“ so Konrad.
Und der dritte herausfordernde Aspekt: Die bei Diehl Aviation eingesetzten Roboteranlagen entsprachen nicht exakt den seitens des Herstellers bereitgestellten Messwerten und digitalen Modellen. Die richtigen Null-Punkte, Parameter oder auch Verschiebungen auf der Anlage, die sich über den Aufbau und auch die Kalibrierung ergeben haben, galt es im Nachgang zu korrigieren und beide – das reale und das digitale Modell – entsprechend genau abzugleichen. „Dieser Prozess war sehr herausfordernd und ein gravierender Lernschritt für uns alle. Hier mussten wir dann auch mehr Zeit als erwartet investieren“, stellt Böhringer rückblickend fest.
Ein weiterer Umstand erforderte von allen mehr Zeit und Flexibilität: Wesentliche Schritte des Projekts fielen in die erste Phase der Corona-Pandemie des Jahres 2020. So mussten alle beteiligten Partner Aspekte wie Krankheit, Betriebsschließungen, Lieferverzögerungen und virtuelles Agieren ad hoc in den Projektplan einbeziehen.
Offline-Programmierung in Serienumgebung
Im Dezember 2020 fand ein Treffen aller beteiligten Partner statt, bei dem die bisherigen Schwierigkeiten offen thematisiert wurden. Und bei dem man konstruktiv nach Lösungswegen suchte. So konnte ein Miteinander entstehen, welches die Zusammenarbeit im weiteren Verlauf des Projekts prägte.
Daniel Kohn und Jürgen Böhringer sind sich einig: „Die Stimmung war lösungsorientiert und nach vorne gerichtet. Es ging um die Sache, um die Umsetzung und um die richtige Priorisierung von Ressourcen, um das Ganze abzubilden“.
Im Januar und Februar 2021, hatten die Partner „die letzten Gaps“ geschlossen. Die ersten Programme konnten nun generiert werden. Im April 2021 begannen die Mitarbeiter der Abteilung „Tooling“ bei Diehl Aviation aktiv in Serien-Umgebung, Programme zu schreiben.
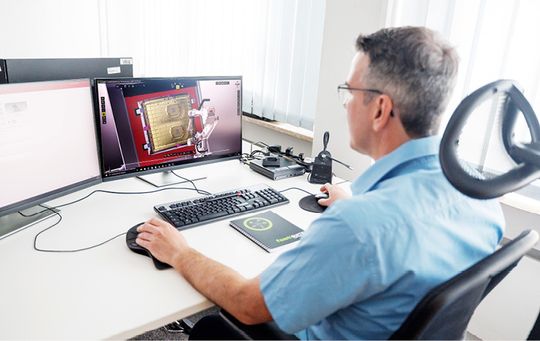
Das Resultat der gemeinsamen Anstrengungen war eine voll funktionsfähige Fastsuite-Lösung, die die Oberflächen-Reinigung vollumfänglich abbilden konnte. Aufgrund des speziellen Charakters des Wasserstrahl-Reinigungsprozesses für die Presswerkzeuge wurde eine Sonderlösung gefunden: Der Reinigungsprozess wurde vom Prinzip her als ein Lackier-Prozess abgebildet – nur nicht mit Material-Auftrag, sondern mit Material-Abtrag. Wichtig dabei sei, dass die Anlage nach der Programmierung komplett ohne Nach-Teachen laufe, betont Daniel Kohn. Denn Simulation im Vorfeld schützt vor Schäden und verkürzt die Optimierungsschleifen. „Im Vergleich zur manuellen Programmierung spart man sich bis zu 2 Stunden Arbeitszeit, mit einem tendenziell laufzeitoptimierten Programm“, so Kohn. Dies, während die Anlage parallel weiterhin in Betrieb ist. „Ohne Offline-Programmierung mit Fastsuite hätten wir Maschinenstillstände, die wir uns bei der steigenden Varianz nicht erlauben können“, weiß Böhringer.
Die benötigten Informationen und CAD-Daten wurden vorab in der benötigten Granularität und vor allem in der richtigen Qualitätsstufe definiert und aufbereitet. So stellte man sicher, dass auch zukünftig die Basis gelegt war, um die größtmögliche Effizienz in der Programmierung und Datenaufbereitung zu haben. „Mittlerweile haben wir zirka 340 Programme mit Fastsuite erstellt. Es hat geflutscht“, lautet Böhringers beherztes Fazit.
Win-win-Situation für beide Seiten
Zeitersparnis und Effizienz sind die Vorteile lauten für Diehl Aviation: Zum einen bezieht sich dies auf die Offline-Programmierung selbst – und zum anderen auf den eigentlichen Reinigungsprozess. Da nun die notwendigen Formate der Catia-Modelle definiert und in der Software enthalten sind, können die Kollegen in der „Tooling“-Abteilung nun eine Vorrichtung in einem Tag programmieren.
Zudem kann die komplette Vorrichtung, dank der Automatisierung, in einer Stunde gereinigt werden. Früher kalkulierte man bei Diehl Aviation mit rund fünf Stunden, da der Prozess der Oberflächenreinigung von Presswerkzeugen sich manuell sehr aufwendig gestaltet. Die Automatisierung bringt somit auch wirtschaftliche Vorteile in Bezug auf Ressourcennutzung mit sich. So konnte der gesamte Reinigungsprozess zeitlich um 40% reduziert werden.
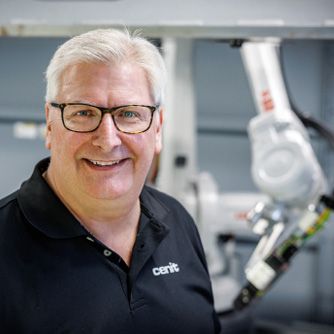
Die beiden anderen Vorteile sind die Qualitäts- und Prozesssicherheit: Die Oberflächen eines Presswerkzeugs sind sehr sensibel. Deswegen sind Abläufe so zu programmieren, dass die Roboteranlagen mit einer stets gleichbleibend hohen Qualität die Oberflächen reinigen. Dies wird bei der Offline-Programmierung durch die Angabe von Parametern für die entsprechenden Haltepunkte standardisiert sichergestellt. Auch kann vorab in der Simulation eine Kollisionskontrolle durchgeführt werden. Mit einer manuellen Programmierung, also mit dem klassischen Teachen, ließe sich nicht überprüfen, ob die Oberfläche eventuell geschädigt würde. Denn Teachen ist letztendlich „Augenmaß“.
„Bei uns verlässt kein NC-Programm und kein Roboter-Programm die „Tooling“-Abteilung, ohne dass sie auf Kollision geprüft sind und entsprechend auch Maschinenbeschädigungen ausgeschlossen werden können. Das ist einer der Hauptgründe, warum an einer Offline-Roboter-Programmierung mit Fastsuite kein Weg vorbeiführt“, folgert Böhringer.
An fachlicher Expertise bei der Offline-Programmierung gewonnen
Und was war nun der fachliche Mehrwert für Cenit? Der Zugewinn an fachlicher Expertise in Bezug auf die Oberflächen-spezifische Programmierung. Was nüchtern klingt, ist ein enormer Vorteil für einen Software-Hersteller: Denn das Thema Oberflächenprogrammierung ist ein Spezialgebiet, das gefragt ist. „In der Zusammenarbeit mit den Projekt-Kollegen bei Diehl Aviation durften wir viel über die Spezifika dieses Prozesses lernen und haben diese als neue Funktionalitäten in Fastsuite E2 eingebracht. Dies bringt unserem Kunden Diehl Aviation konkreten Mehrwert in Bezug auf seine Roboter-Prozesse – und erhöht die Funktionalität der Software insgesamt“, so Konrad.
Auch über das Fachliche hinaus, so betonen Cenit und Diehl Aviation, haben sich im Rahmen der Zusammenarbeit beide Seiten weiterentwickelt und profitieren von der Partnerschaft. Man versteht sich und handelt als Partner auf Augenhöhe, die ein gemeinsames Ziel vorfolgen. Und dies ist entscheidend für den gemeinsamen Erfolg.