Schnellere Produkteinführung durch virtuelle Inbetriebnahme
Anbieter zum Thema
Der Druck, die Kundenerfahrung zu verbessern und die Rentabilität zu steigern, nimmt stetig zu. Viele Unternehmen reagieren darauf mit digitaler Transformation und revolutionieren ihre Geschäftsmodelle mit neuen Wertversprechen. Mit modernen Technologien wie der Digital-Twin-Software Emulate3D können Hersteller eine Produktionszelle, ein komplettes Produktionssystem oder eine Fertigungsstraße simulieren und virtuell in Betrieb nehmen, noch bevor die erste Leiterplatte verbaut wird.
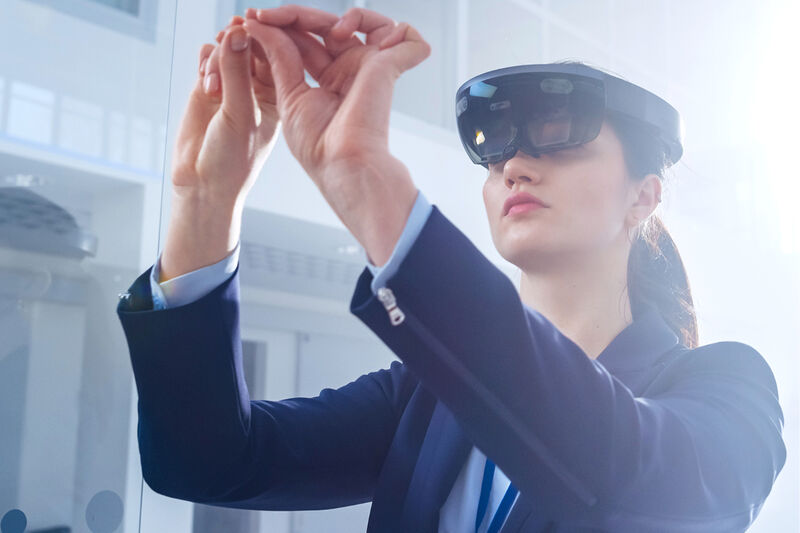
Laut Nicola Iovine, Strategic Business Developer EMEA, Digitales Design und SaaS bei Rockwell Automation, wird die Einführung der Digital-Twin-Technologie vor allem durch drei Faktoren bedingt. „Erstens geht es um Kostenreduktion, insbesondere die der Energiekosten. Virtuelle Inbetriebnahmen und Tests sind da ein großer Vorteil“, so Iovine. „Der zweite Faktor ist das Arbeiten im Homeoffice oder an anderen Standorten, ohne die physische Anwesenheit vor Ort. Dies wurde während der Pandemie sehr zu schätzen gelernt. Und schließlich ist auch Nachhaltigkeit ein wichtiger Punkt. Für Tests wird eine erhebliche Menge an Material und Energie benötigt. Dieser Aufwand lässt sich durch virtuelle Tests reduzieren.“
Dynamische Konstruktion, in der physikalische Gesetze herrschen
Mit einem dynamischen und digitalen Zwilling können Maschinenbauer ihre Maschinen testen, schon bevor diese gebaut werden. „Der Entwurf einer Maschine beginnt normalerweise mit einem mechanischen oder elektrischen CAD“, erklärt Iovine. „Durch Hinzufügen von Konfigurationen und Kinematik wird das mechanische CAD dynamisch und ist nicht nur eine digitale Kopie oder ein digitales Modell. Es handelt sich also nicht nur um eine 3D-Ansicht der Maschine, sondern um eine dynamische Konstruktion, in der physikalische Gesetze herrschen. Man kann sich darin bewegen, die gesamte Maschine testen oder Produkte verpacken.“
Dieser Ansatz ist für einzelne Maschinen ebenso sinnvoll wie für eine Produktionszelle oder eine vollständige Fertigungslinie. „Bei der Integration von Maschinen in eine Produktionsstraße stellt normalerweise jeder Maschinenbauer seinen digitalen Zwilling bereit, der dann in den digitalen Zwilling der kompletten Produktionsstraße integriert wird“, fügt Nicola hinzu. „Auf diese Weise kann der Durchsatz getestet werden. Außerdem lassen sich etwaige Engpässe zwischen Maschinen ermitteln. Es ist ein Ökosystem aus Maschinenbauern, Systemintegratoren und Ingenieurbüros.“
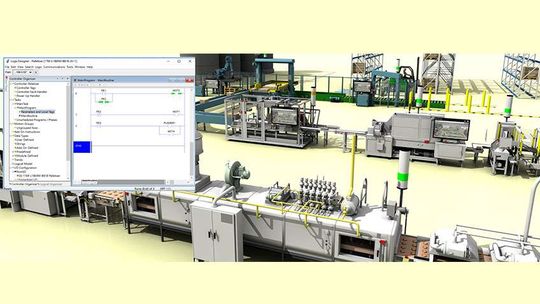
Fortschrittliche Digital-Twin-Technologien
Virtuelle Inbetriebnahmen oder Steuerungstests sind fester Bestandteil fortschrittlicher Digital-Twin-Technologien. Dabei werden das Automatisierungssystem und die SPS-Codes überprüft. „Sobald das digitale Modell erstellt ist, kann die virtuelle Inbetriebnahme beginnen. Dabei spielt es keine Rolle, ob die Maschine bereit ist oder ob noch Komponenten fehlen“, fährt Nicola fort. „Der SPS-Code kann am digitalen Modell wie auf der realen Maschine getestet werden, da das digitale Modell das Verhalten der physischen Maschine nachahmt.“
Nacharbeiten vermeiden und Fehler minimieren
Jede Phase des Entwicklungsprozesses stellt unterschiedliche Anforderungen an die Software für dynamische Modellierung. Da sich Projekte von der Präsentation und Durchsatzanalyse bis zur Installation und Inbetriebnahme weiterentwickeln, können durch die Integration des typischen Arbeitsablaufs in die Simulationssoftware Nacharbeiten vermieden und Fehler minimiert werden. „Alles beginnt mit der Konstruktion der Maschine, gefolgt von der Inbetriebnahme und schließlich von Betrieb und Wartung“, erklärt Nicola. „Das digitale Modell ist keine einmalige Sache. Es ist dynamisch und kann in allen verschiedenen Phasen verwendet werden.
„Es kann als Hilfsmittel Vertriebsmitarbeiter dabei unterstützen, Konzept und Design einer neuen Maschine darzustellen. Der Durchsatz kann simuliert und die Inbetriebnahme virtuell durchgeführt werden. Aber das ist noch nicht alles: Das digitale Modell lässt sich zur Bedienerschulung einsetzen, bevor die Maschine physisch verfügbar ist. Und schließlich kann es auch eine wertvolle Hilfe bei der Wartung sein. Es deckt den gesamten Lebenszyklus der Maschine ab und spiegelt den aktuellen Zustand genau wider.“
Erfahren Sie hier, wie Unternehmen ihre Digitalisierung voranbringen ...
Teaser-Bild: Neue Möglichkeiten: Kombination eines digitalen Zwillings mit Augmented-Reality-Headsets.
(Bild: Rockwell Automation)