Simulations-App selbst entwickeln: Profi für Multiphysik-Simulation macht es möglich
Anbieter zum Thema
Additive Fertigungsprozesse wie die Metallpulverbettfusion ermöglichen eine schnelle und anpassungsfähige Produktion hochwertiger Komponenten. Das britische Manufacturing Technology Centre hat zusammen mit Partnern aus der Luft- und Raumfahrtindustrie eine Anlage für die Pulverbettfusion gebaut und ein Simulationsmodell sowie eine App entwickelt, mit denen die Mitarbeiter der Anlage fundierte Entscheidungen über den Betrieb treffen können.
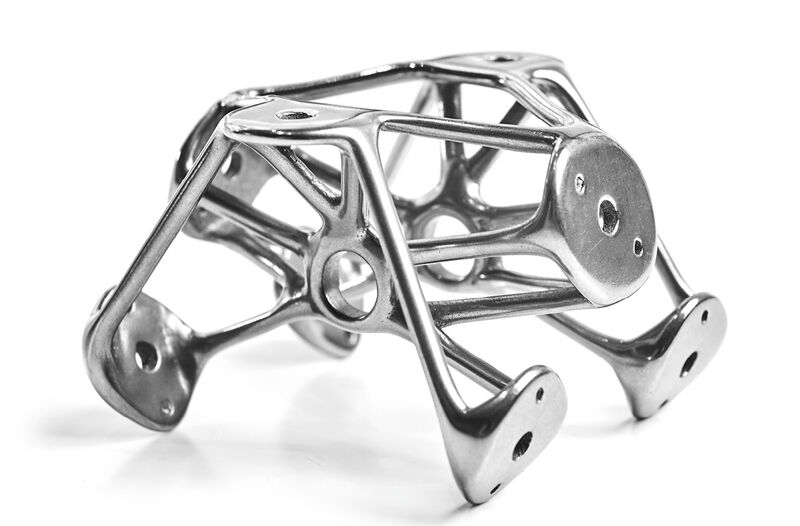
Simulations-App in der Praxis: Um britischen Fabriken zu helfen, mit der Welt Schritt zu halten, fördert das Manufacturing Technology Centre (MTC) die moderne Fertigung im gesamten Vereinigten Königreich. Das MTC hat seinen Sitz in der historischen englischen Industriestadt Coventry, aber sein Blick ist ausschließlich auf die Zukunft gerichtet. Deshalb hat das Team um Adam Holloway, Technology Manager bei MTC, erhebliche personelle und technische Ressourcen für sein National Centre for Additive Manufacturing (NCAM) bereitgestellt.
Simulations-App für die additive Fertigung
Das NCAM-Projekt Digital Reconfigurable Additive Manufacturing for Aerospace (DRAMA) bietet einen geeigneten Rahmen für diese Erkundung. Zur DRAMA-Initiative, die in Zusammenarbeit mit zahlreichen Herstellern entwickelt wurde, gehört auch die bereits erwähnte neue Anlage für die Pulverbettfusion. Mit dieser Minifabrik spielen Holloway und seine Simulationskollegen eine wichtige Rolle, um die Produktion von additiv gefertigten Komponenten für die Luft- und Raumfahrt zum Erfolg zu führen.
Wie Wärme und Feuchtigkeit die Metallpulverbettfusion beeinflussen
„Die Marktchancen von Methoden der additiven Fertigung (AF) sind seit langem bekannt, aber es gab viele Hindernisse für eine groß angelegte Einführung“, sagt Holloway. „Einige dieser Hindernisse können während der Entwicklungsphase von Produkten und AF-Anlagen überwunden werden. Andere Probleme, wie zum Beispiel Auswirkungen der Umweltbedingungen auf die AF-Produktion, müssen angegangen werden, während die Anlage in Betrieb ist.“
So ist beispielsweise die sorgfältige Kontrolle von Wärme und Feuchtigkeit eine wesentliche Aufgabe für das DRAMA-Team. „Das Metallpulver, welches für das Pulverbettfusionsverfahren zum Einsatz kommt, reagiert sehr empfindlich auf äußere Bedingungen“, sagt Holloway. „Dies bedeutet, dass es bereits während der Lagerung zu oxidieren beginnt und Feuchtigkeit aus der Umgebung aufnehmen kann. Diese Prozesse setzen sich während des Transports durch die Anlage fort. Wenn das Metallpulver Wärme und Feuchtigkeit ausgesetzt ist, verändert sich sein Fließverhalten, sein Schmelzverhalten, seine elektrische Ladung und seine Verfestigung“, erklärt er. „All diese Faktoren können sich auf die Qualität der zu produzierenden Bauteile auswirken.“
Interaktives Prozessmanagement mit Multiphysik-Modellierung
Der Einsatz von Multiphysik-Simulation für ein sorgfältiges Prozessmanagement kann eine kosteneffiziente Alternative darstellen. „Im Rahmen des DRAMA-Programms haben wir ein Modell unserer Anlage mithilfe der Funktionen für computergestützte Fluiddynamik (CFD) der Comsol-Software erstellt. Unser Modell verwendet die Finite-Elemente-Methode, um partielle Differentialgleichungen zu lösen, die den Wärmetransport und die Fluidströmung im Luftbereich unserer Anlage beschreiben“, betont Holloway. „So konnten wir untersuchen, wie die Umgebungsbedingungen durch verschiedene Variablen beeinflusst werden – vom Wetter draußen über die Anzahl der in Betrieb befindlichen Maschinen bis hin zur Positionierung der Maschinen in der Fabrikhalle. Ein Modell, das diese Variablen berücksichtigt, hilft dem Fabrikpersonal, die Belüftung und die Produktionspläne anzupassen. Damit lassen sich die Bedingungen optimieren“, erklärt er.
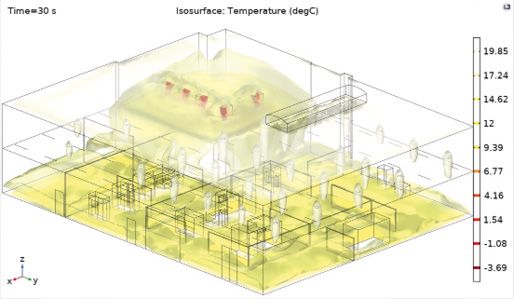
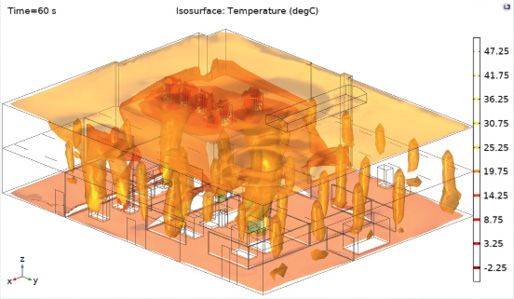
Eine Simulations-App für das Fabrikpersonal
Das DRAMA-Team hat sein Modell zugänglicher gemacht, indem es mit dem Application Builder von Comsol Multiphysics eine Simulations-App dafür erstellt hat. „Wir versuchen, die Ergebnisse einiger sehr komplexer Berechnungen einfach und verständlich darzustellen“, erklärt Holloway. „Die Entwicklung einer App aus unserem Modell ermöglicht es den Mitarbeitern, während ihrer täglichen Arbeit Vorhersagesimulationen auf Laptops durchzuführen.“
Der App-Nutzer kann relevante Randbedingungen für den Beginn einer Fabrikschicht festlegen und dann fortlaufend Anpassungen vornehmen. Im Laufe einer Schicht werden Wärme- und Luftfeuchtigkeitswerte unweigerlich schwanken. Möglicherweise sollte das Fabrikpersonal den Produktionsplan ändern, um die Qualität der Bauteile aufrechtzuerhalten, oder vielleicht müssen einfach nur Türen und Fenster geöffnet werden, um die Belüftung zu verbessern. Nutzer können die Einstellungen in der App ändern, um die möglichen Auswirkungen solcher Maßnahmen zu testen.
Simulations-App ermöglicht digitalen Zwilling auf Fabrikebene
Die aktuelle Simulations-App ist zwar ein wichtiger Schritt nach vorn, aber sie erfordert immer noch die manuelle Eingabe relevanter Daten durch die Mitarbeiter. Mit Blick auf die Zukunft stellt sich das DRAMA-Team etwas Integraleres und damit Leistungsstärkeres vor: Einen „digitalen Zwilling“ für seine AF-Anlage. „Um unser Modell der Fabrikumgebung zu einem digitalen Zwilling zu machen, versorgten wir es zunächst mit Live-Daten aus der tatsächlichen Fabrik“, erklärt Holloway. „Sobald unser Fabrikmodell im Hintergrund lief, war es in der Lage, seine Vorhersagen als Reaktion auf die Daten, die es erhielt, anzupassen und auf der Grundlage dieser Vorhersagen bestimmte Aktionen vorzuschlagen. Wir wollen unser Vorhersagemodell in eine Feedback-Schleife integrieren, die die eigentliche Fabrik und ihre Mitarbeiter einbezieht. Das Ziel ist ein ganzheitliches System, das auf die aktuellen Bedingungen in der Fabrik reagiert, das Simulation nutzt, um Vorhersagen über die zukünftigen Bedingungen zu treffen, und das auf der Grundlage dieser Vorhersagen nahtlos selbstoptimierende Anpassungen vornimmt“, sagt Holloway. „Dann werden wir tatsächlich sagen können, dass wir einen digitalen Zwilling unserer Fabrik erstellt haben.“
Abgesehen von den praktischen Erkenntnissen für die Hersteller bietet das Projekt auch eine weiterreichende Lektion: Durch die Kopplung der Produktionslinie mit einem dynamischen Simulationsmodell hat das DRAMA-Projekt den gesamten Betrieb sicherer, produktiver und effizienter gemacht. Das DRAMA-Team hat dies erreicht, indem es das Modell dort eingesetzt hat, wo es am meisten bewirken kann – in den Händen der Menschen, die in der Fabrikhalle arbeiten.
Der Autor Alan Petrillo ist Content Writer bei Comsol.