So sieht das erste Strahltriebwerk aus dem 3D-Drucker aus
Anbieter zum Thema
PTC hat das (laut eigenen Angaben) weltweit erste vollständig 3D-gedruckte Mikro-Turbotriebwerk vorgestellt. Es wurde in der CAD-Software Creo entwickelt und ist eine einzige, vollständige Baugruppe, inklusive aller rotierenden und fixen Komponenten. Das Triebwerk wurde mit einem 3D-Drucker von EOS aus Inconel gedruckt und wiegt nur 3,6 Kilogramm.
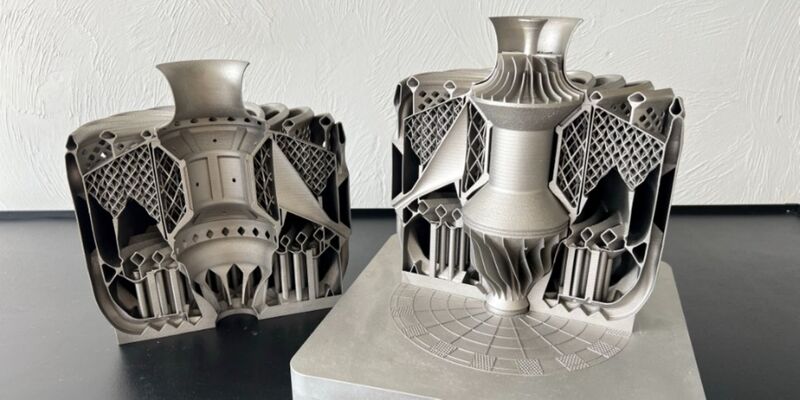
Die Entwicklung und der 3D-Druck eines vollständig selbsttragenden Mikro-Turbotriebwerks inklusive Turbine mit 50.000 Umdrehungen pro Minute, das keine Montage erfordert, markiert einen Durchbruch bei der Konstruktion für die additive Fertigung. Bislang sind für derartige Motoren komplexe Montageprozesse und viele, oft teure Komponenten nötig. Das stellt die Hersteller vor Herausforderungen hinsichtlich der Lieferkette und der Verfügbarkeit von Teilen. Zudem müssen sie Sorge tragen, das Fachwissen und die Fähigkeiten zur Herstellung dieser hochpräzisen Baugruppen im eigenen Haus zu halten. Durch die additive Fertigung entfällt mit dem Montageprozess auch der Bedarf an Komponenten und Werkzeugen. Das reduziert die Kosten und ermöglicht eine On-Demand-Fertigung direkt beim Kunden vor Ort.
Triebwerk aus dem 3D-Drucker war ein Gemeinschaftsprojekt
Das vollständig 3D-gedruckte Triebwerk ist das Ergebnis eines Projekts, das von Ronen Ben Horin, VP of Technology bei PTC und Senior Research Fellow am Technion – Israel Institute of Technology, und Beni Cukurel, außerordentlicher Professor für Luft- und Raumfahrt am Technion konzipiert und geleitet wurde. Es erforderte jahrelange intensive wissenschaftliche Forschung auf dem Gebiet des Strahlantriebs und umfangreiches Fachwissen zu innovativer Triebwerkstechnik und dem Design für die additive Fertigung.
Creo, die 3D-CAD-Lösung von PTC, wurde vor allem wegen ihrer innovativen Konstruktionsfunktionen für das Projekt ausgewählt, darunter:
Leichtbauweise: Creo ermöglicht eine anspruchsvolle Gittermodellierung und ein generatives Design zur Material- und Gewichtsreduzierung bei derselben Festigkeit und Leistung wie sie Konstruktionen mit mehr Material und höherem Gewicht aufweisen.
Selbsttragende Geometrien für den 3D-Druck: Balkenbasierte Gitter optimieren Konstruktionen automatisch für den 3D-Druck. Creo unterstützt auch selbsttragende formelgesteuerte Gitter, die mit Druckbarkeitsprüfungen und Modifikatoren kombiniert werden können, um das Design für einen effizienten 3D-Druck anzupassen.
Interoperabilität mit 3D-Druckern: Creo ist mit den meisten 3D-Druckern sowohl zum Drucken als auch zum Nachbearbeiten kompatibel. Die 3D-Komponentenkonstruktion in Creo ist entscheidend für die Durchführung traditioneller Bearbeitungen zur präzisen Montage. Creo bietet eine Vielzahl von Formaten, inklusive 3MF, um 3D-Modelle an die verschiedenen Drucktechnologien zu senden, und ermöglicht Anwendern, assoziative Modelle für Bearbeitungsvorgänge auf einfache Weise zu erstellen.
Lesen Sie auch: Elektrogreifer: Smarter Umgang mit empfindlichen Gütern