Materialauswahl vor Simulation: Produktentwicklung neu gedacht
Anbieter zum Thema
Viele glauben, dass die Simulation bei der Materialauswahl hilft, aber eigentlich es ist andersherum: Die Materialauswahl vor der Simulation trägt dazu bei, Produkte zu verbessern, Nachhaltigkeitsziele zu erreichen und Kosten zu senken.
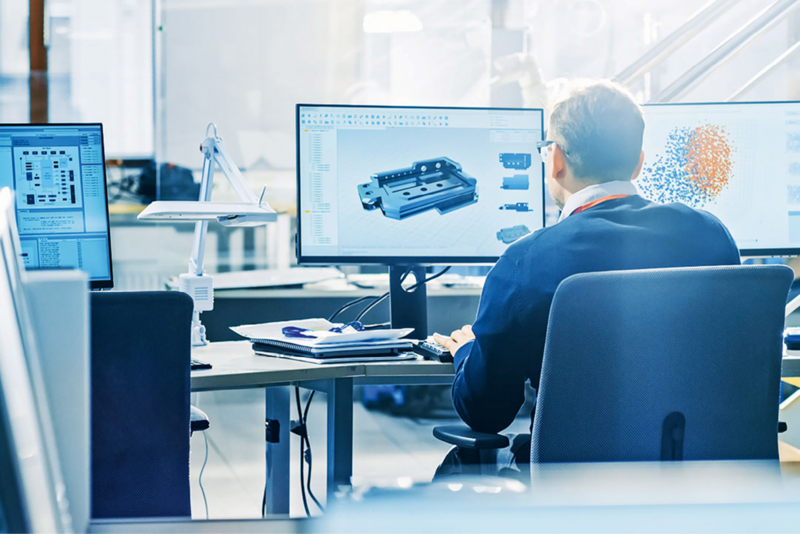
Materialauswahl first: Historisch gesehen war die Modellierung von Werkstoffen noch nie eine einfache Aufgabe. Für jedes Material in einem Modell müssen Koeffizienten oder Werte bestimmt werden, um das Verhalten des Materials möglichst genau nachzubilden. Zu den Materialeigenschaften gehören Wärmeausdehnung, Schlagfestigkeit, Leitfähigkeit, Dichte und vieles mehr, je nach Verwendungszweck. In der Regel erfordert der Prozess die Hilfe von Kalibrierung, Berechnung und einer beträchtlichen Menge von Trial-and-Error, um den jeweils besten Satz von Materialkoeffizienten zu bestimmen.
Zur Analyse des Verhaltens dieser Materialien und der optimalen Zusammenstellung – in der Regel Legierungen, Elastomere oder Polymere – wird häufig Simulation eingesetzt. Auf der Grundlage der Simulationsergebnisse und der Materialreaktion werden die geeigneten Materialmodelle ausgewählt, um die Rohstoffe weiter zu bewerten, die Produktleistung zu überprüfen und die Effizienz zu beurteilen.
Materialauswahl steht vor der Simulation
Die Genauigkeit der Simulation hängt von der Qualität der Informationen über die Materialeigenschaften ab. Der Zugang zu genauen Informationen über Materialeigenschaften kann jedoch schwierig sein. Genaue Werte zu Faktoren wie Festigkeit, Haltbarkeit, Schadenstoleranz und Gewicht sind von entscheidender Bedeutung, denn selbst winzige Fehler können große Auswirkungen auf die Simulationen haben und im weiteren Verlauf des Produktentwicklungsprozesses zu großen Problemen führen. Die Materialauswahl fließt als erstes in eine Simulation ein und macht sie zu einem entscheidenden ersten Schritt jeder Produktentwicklung.
Die Finite-Elemente-Analyse (FEA) ist eine Technik, die die Reaktion einer Struktur auf bestimmte Belastungsbedingungen simuliert. Während des Konstruktionsprozesses können Ingenieure computergestützte Konstruktionszeichnungen (CAD) erstellen und die Lasten simulieren, um die Spannungskonzentrationen und Verformungen eines Teils zu verstehen. Auf diese Weise erhalten die Ingenieure detaillierte Materialanforderungen auf Grundlage aller Abmessungen und Konstruktionsparameter.
Die Sicherstellung genauer und geeigneter Materialdaten ist daher ein wichtiger Schritt bei jeder mechanischen, fluidtechnischen, elektrischen und additiven Fertigungssimulation. In der Tat gibt es kaum eine Simulationsart, die nicht von Materialintelligenz-Tools profitieren würde. Daher müssen Ingenieure und Konstrukteure besser verstehen, wie sich die Materialauswahl auf ihre Produktentwicklung auswirkt.
Unnötige Kosten vermeiden
Der Großteil aller Kosten bei der Herstellung komplizierter Produkte fällt bereits in der Entwurfsphase an. Das liegt daran, dass das Geld für die Ausrüstung und für den Raum, in dem das Produkt hergestellt werden soll, bereits ausgegeben ist, bevor es an die eigentliche Herstellung geht. Daher sollten bereits früh in der Designphase Entscheidungen über die Materialien getroffen werden.
Ein zusätzlicher Faktor ist die Zeitersparnis, die Simulation mit sich bringt. Da Entscheidungen zu Materialien und Design bereits zu Beginn richtig getroffen werden, entfällt die Notwendigkeit zahlreicher physischer Tests.
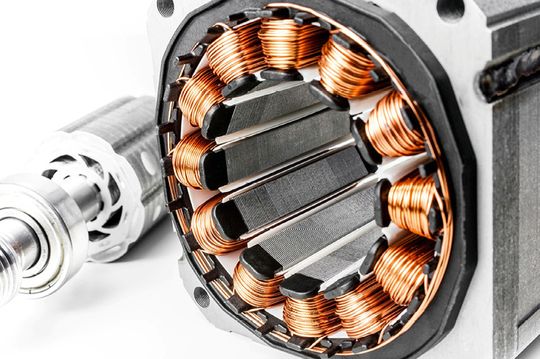
Öko-Audit spart Zeit und Kosten
Eco-Design bedeutet, dass Umweltaspekte in allen Phasen des Produktentwicklungsprozesses eine zentrale Rolle spielen. Beispielsweise wird in der Luft- und Raumfahrtindustrie der größte Teil aller produktbezogenen Umweltauswirkungen in der Konzeptionsphase festgelegt, in der Entscheidungen über Werkstoffe und Fertigung getroffen werden. Findet man die inhärenten Nachhaltigkeitseigenschaften von Materialien sehr früh heraus, kann dies dementsprechend große Auswirkungen auf die Gesamtnachhaltigkeit eines Produkts haben. Genaue Daten zur Materialauswahl geben Aufschluss darüber, ob das finale Produkt Schadstoffe enthält, wie es um seine Energie und CO2-Emissionen bestellt ist, ob es Konfliktmaterialien oder seltene Metalle enthält und vieles mehr.
Auch Lebenszyklusanalysen (LCA) werden immer häufiger durchgeführt. Dabei handelt es sich um eine End-to-End-Analyse, die ein Hersteller durchführen muss, um die potenziellen Auswirkungen eines Produkts auf die Umwelt zu bestimmen. Das schließt vorgelagerte und nachgelagerte Materialien und Prozesse sowie Nutzungs- und Entsorgungsphasen ein. Diese Analysen können Zehntausende von Euro kosten und mehrere Wochen dauern. Die Durchführung eines Öko-Audits für die vorgesehenen Materialien und Prozesse vor der Durchführung einer LCA kann diese Kosten reduzieren und viel Zeit und Geld sparen.
Die Kontrolle bei der Materialauswahl behalten
Oft ändern sich Vorschriften oder Lieferketten werden unterbrochen. Mit einer effektiven Materialauswahl können Unternehmen auf diese Situationen reagieren. Wenn ein Material nicht mehr verfügbar ist, können sie abschätzen, welche Alternativen verwendet werden können und wie effektiv diese als Ersatz sein werden. Durch die Kenntnis der zu verwendenden Materialien oder ihrer Alternativen und ihrer genauen Eigenschaften, können die Unternehmen zudem effizienter mit Lieferanten zusammenarbeiten. Statt fragen zu müssen „wie ist dieses Material, wie wird es reagieren, wie viel wird es kosten?“ können sie dem Lieferanten genau sagen, was sie brauchen.
Es gibt aber auch Hersteller, die nicht mit Rohstoffen arbeiten, sondern mit zugekauften Teilen, und daher nicht wissen, um welche Materialien es sich handelt. Bei Fahrzeugen mit digitalen Bildschirmen ist zum Beispiel der Hersteller, der den Bildschirm in das Fahrzeug einbaut, dafür verantwortlich, dass er konform ist. Nicht der Hersteller des Bildschirms. In diesem Fall muss der Erstausrüster Erklärungen der Lieferanten über die Materialien einholen. Zum Beispiel. ob es eingeschränkte Stoffe sind oder ob es sich um konfliktfreie Materialien handelt. Die Hersteller müssen unbedingt die in diesen Komponenten verwendeten Materialien identifizieren, um bei Kaufentscheidungen ein größeres Bewusstsein zu schaffen.
Werkstoffe nicht vernachlässigen
Erst mit genauen Materialdaten können Unternehmen ihre Produkte richtig simulieren. Simulation bietet ein großes Potenzial, die Produktentwicklung in allen Branchen und Phasen zu unterstützen und zu erleichtern. Oft wird jedoch das Potenzial der Materialienauswahl in der Simulation übersehen oder nicht ausreichend genutzt. Bereits in dieser Phase unterstützt Simulation, indem Kosten gesenkt, die Time-to-Market reduziert und Produkte leistungsfähiger und umweltfreundlicher gestaltet werden können. Im Hinblick auf das ECO-Design wird Simulation immer wichtiger und entlang der gesamten Produktentwicklung zum Einsatz kommen.
Der Autor Scott Wilkins ist Lead Product Marketing Manager bei Ansys.
Lesen Sie auch: Model-Based-Twin-Engineering: Wie es funktioniert