PLM-Lösung: Innovative Software für innovative Produkte
Anbieter zum Thema
Was haben ein Flughafen in Zürich, ein Bikepark in Norwegen und ein Motorsportrundkurs auf der indonesischen Insel Lombok gemeinsam? Auf allen drei Baustellen kamen Verdichtungsgeräte von Bomag zum Einsatz. Das Unternehmen hat jetzt seine CAD/PLM-Welt neu ausgerichtet.
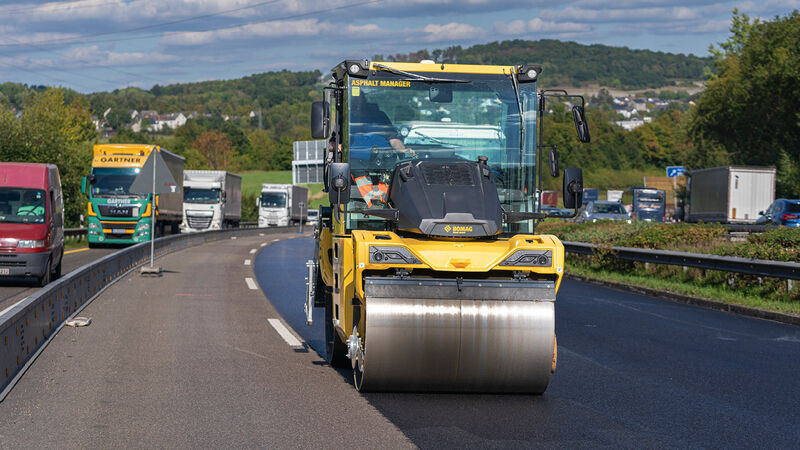
PLM-Lösung im Einsatz: Schon seit 1957 entwickelt und fertigt Bomag mit Hauptsitz im rheinland-pfälzischen Boppard Maschinen, mit denen sich Erde, Asphalt und Müll verdichten lassen. Hinzu kommen Stabilisierer und Recycler, Fräsen und Straßenfertiger. Außerdem bietet das Unternehmen passende digitale Lösungen an und trägt mit all dem zu einem effizienten und verantwortungsvollen Ausbau von Straßen und Verkehrsinfrastrukturen bei. Heute umfasst das Portfolio mehr als 250 unterschiedliche Produkte mit unzähligen Optionen – von der vorwärtslaufenden Vibrationsplatte, die nur 47 Kilogramm wiegt bis zum 56,6 Tonnen schweren Müllverdichter.
PLM-Lösung: Innovative Produkte dank innovativer Software
Als globaler Hersteller und Taktgeber der Branche geht Bomag heute mit digitalen Services für die vernetzte Baustelle voran und bringt regelmäßig Innovationen auf den Markt, zu Beispiel das neue Bedien- und Kabinenkonzept myCockpit für schwere schemelgelenkte Tandemwalzen oder Stampfer und leichte Tandemwalzen mit Akkuantrieb. Die mehr als 150 Entwicklerinnen und Entwickler an allen Standorten von Bomag arbeiten stetig an neuen Produkten, die durch den Einsatz neuer Technologien die Anforderungen der Kunden immer besser erfüllen. Die Herausforderung ist dabei, der wachsenden Dynamik gerecht zu werden und immer kürzere Innovationszyklen zu erreichen.
Um die Arbeit der Entwicklerinnen und Entwickler zu unterstützen, hat das Unternehmen schon in den 1990er-Jahren die erste 3D-CAD-Lösung eingeführt. Ab Mitte der 2000er-Jahre kam dann außerdem SAP ERP samt PLM-Modul zum Einsatz, wobei die bestehende CAD-Lösung integriert wurde. Diese Architektur führte zu Problemen, als die Verantwortlichen bei Bomag beschlossen haben, SAP ERP (SAP ECC 6.0) durch SAP S/4HANA abzulösen, weil SAP S/4HANA die bestehende Integration nicht unterstützt. „Hinzu kam, dass ohnehin eine komplette Neuausrichtung der CAD/PLM-Welt erfolgen sollte, um die im Laufe der Jahre stetig gewachsenen Anforderungen besser erfüllen zu können. Deshalb entschieden wir uns, eine neue CAD/PLM-Landschaft einzuführen“, erläuterte Dr. Stefan Forkert, Vice President Engineering bei Bomag.
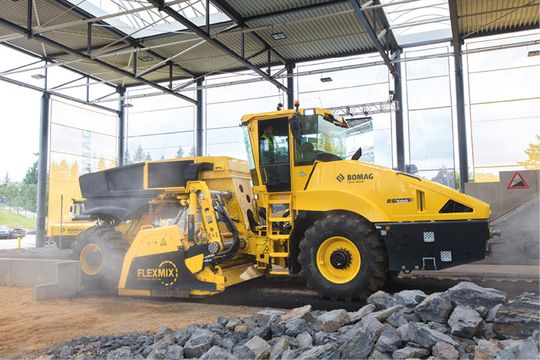
IT-Auswahl anhand von 50 konkreten Use Cases
Bomag befragte in Workshops systematisch die Mitarbeiterinnen und Mitarbeiter, die täglich die CAD- und PLM-Lösung nutzen. Auf diese Weise ließen sich insgesamt 500 Anforderungen identifizieren, die dann zu 50 Use Cases zusammengefasst wurden, beispielsweise „Biegen, Umformen“, „Freiformflächen“ oder „Prozesse, Rollen, Rechte“. Jeder Use Case wurde auf Basis der Parameter „Rolle“, „Auslöser“, „Vorbedingungen“ und „Erfolgsfaktoren“ bewertet. Beim Use Case „Biegen, Umformen“ etwa ist der Konstrukteur die relevante Rolle, die Neukonstruktion ist der Auslöser. Wichtige Vorbedingung ist, dass im CAD-System die Norm für das Biegen hinterlegt ist. Und zu den Erfolgsfaktoren gehört unter anderem, ein Blechteil direkt modellieren oder auf Basis eines 3D-Volumenmodells ableiten zu können. Mit diesen sehr klaren definierten Anforderungen ist der Maschinenbauer auf Anbieter von CAD- und PLM-Lösungen zugegangen.
Dazu bat das Unternehmen führende Anbieter von CAD- und PLM-Software, live zu demonstrieren, wie sich eine Auswahl der definierten Use Cases im jeweiligen System umsetzen lassen. Schließlich fiel die Wahl auf Siemens NX als CAD-Lösung und Siemens Teamcenter als PLM-Lösung. „Diese Entscheidung war nicht das Ergebnis einer subjektiven Einschätzung weniger Verantwortlicher. Wir haben die vorgestellten CAD- und PLM-Lösungen von den künftigen Nutzerinnen und Nutzern anhand eines umfassenden Kriterienkatalogs beurteilen lassen und daraus dann für jeden Bereich ein objektives Scoring erstellt“, so Dr. Stefan Forkert.
Schlagkräftiges Projektteam und agiles Vorgehen dank PLM-Lösung
Die Siemens-Lösungen NX und Teamcenter sollten gleichzeitig und innerhalb von nur zwei Jahren eingeführt werden. Angesichts dieses ambitionierten Vorhabens legte Bomag großen Wert darauf, das Projekt sehr solide aufzusetzen. Deshalb hat man ein schlagkräftiges Projektteam etabliert: neben vier Entwicklern, die vollständig für die Implementierung abgestellt waren, gehörten dem Team zehn Mitarbeitende aus den Abteilungen Engineering System Support und IT-Systeme/Tools sowie ein Projektleiter an. Besonders hilfreich war außerdem, dass die einzelnen Teammitglieder ihre individuellen Fähigkeiten und ihr spezifisches Know-how einbrachten. Dadurch ließen sich die externen Partner optimal steuern und es konnte sichergestellt werden, dass von Anfang an alle Rädchen bei der PLM-Lösung perfekt ineinandergriffen. Und schließlich wurden im Laufe des Projekts immer wieder Key User hinzugezogen, die bei speziellen Aspekten – wie der Modellierung von Freiformflächen – unterstützten.
Neben dem ambitionierten Zeitplan war eine wesentliche Herausforderung, dass zum Start lediglich der Zielkorridor klar war, die Umsetzung sich aber noch nicht vollständig spezifizieren ließ. Um mit dieser Unklarheit umzugehen, entschied sich das Projektteam für ein agiles Vorgehen. In 14-tägigen Sprints bearbeiteten die einzelnen Teammitglieder ihre Tasks, aus denen sich oft neue Tasks für den nächsten Sprint ergaben. Wenn abgearbeitete Tasks zu konkreten Spezifizierungsanforderungen führten, wurden diese an die Expertinnen und Experten bei Siemens übergeben, die dann die Lösungen entsprechend implementierten. „Insgesamt haben wir in 30 Sprints über 1.500 Tasks formuliert“, sagt Roland Hecker, Teamleiter PLM-Applikationen und -Prozesse bei Bomag. „Im Grunde konnten wir das gesamte Projekt während der Corona-Pandemie umsetzen, mussten aber mit den sich daraus ergebenden Einschränkungen umgehen und haben quasi ausschließlich remote gearbeitet.“ Um die große Menge an Tasks zu organisieren, kam die Projektmanagementlösung Jira von Atlassian zum Einsatz. Die Software ermöglichte, mithilfe von Boards die Struktur des Projekts abzubilden, was den Überblick erheblich erleichterte.
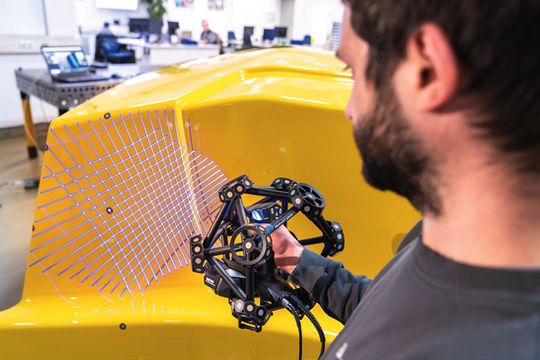
Klare Entscheidungen und vorbildliche Projektkommunikation
Relevant für den Erfolg war auch, dass das Projektteam in Bezug auf die inhaltliche Gestaltung des Projekts und der Verteilung der verschiedenen Aufgaben frühzeitig einige Entscheidungen mit erheblichen Auswirkungen getroffen hatte. Dazu gehörte unter anderem, ausschließlich mit internen Ressourcen ein Konzept für die Migration der Bestandsdaten auszuarbeiten, dann eine Routine für die Migration zu programmieren und zuletzt die Migration durchzuführen. Dadurch ließen sich viele Besonderheiten beim Aufbau der Modelle direkt berücksichtigen. Eine bewusste Entscheidung war auch, keine vorhandenen Zeichnungen zu migrieren. Erfahrungen anderer Unternehmen hatten gezeigt, dass bei diesem Vorgehen nachträglich aufwändige Korrekturen notwendig sind. Zeichnungen komplett zu erstellen, würde nicht viel länger dauern, hat aber den Vorteil, dass die Verbindung zu 3D-Modellen direkt vorhanden wäre. Also wurden im Rahmen des Projekts lediglich die Neutralformate übernommen. Ein selbsterstelltes Tool vereinfachte die Neuerstellung der Zeichnungen deutlich, außerdem unterstütze bei dieser Arbeit ein interner Dienstleister der Fayat-Gruppe – dem Mutterkonzern von Bomag.
Darüber hinaus legte das Projektteam großen Wert auf das Change-Management, also den intensiven Austausch mit den künftigen Anwenderinnen und Anwendern. Bereits zu Beginn wurde über Microsoft Teams ein Live-Event zu den Einzelheiten des Projekts und den Zukunftsperspektiven organisiert, an dem alle Entwicklerinnen und Entwickler teilnehmen konnten. Auch alle anderen Beschäftigten wurden regelmäßig über den Projektfortschritt informiert. Im Mai 2022, also ein viertel Jahr vor dem ersten Go-live, begann die Schulung der über 150 Beschäftigen aus der Entwicklung an allen Produktionsstandorten: in 15 Gruppen und jeweils insgesamt zehn Tage lang. Dabei vermittelten Trainer von Siemens bewusst nur die Grundlagen der beiden neuen Lösungen. Zu spezifischen Inhalten folgten bedarfsorientierte Trainings in Kleingruppen, außerdem wurden weiterführende Videos angeboten. Besonderen Wert hat man auf Konstruktionsrichtlinien und Methodenbeschreibungen gelegt, die mehrsprachig zur Verfügung stehen.
PLM-Lösung: Erfolg bei Zeit, Budget und Qualität
Im Sommer 2022 fand wie geplant der Go-live von Siemens NX und Teamcenter am Produktionsstandort in Boppard statt – die Einführung an den Standorten USA, Italien und China folgte sukzessive. All das erreichte Bomag nicht nur gemäß dem Zeitplan, sondern auch innerhalb des Budgets und mit der angestrebten Qualität. Dr. Stefan Forkert „Das ist für uns ein großartiger Erfolg, der allen am Projekt beteiligten Personen zu verdanken ist.“ Schon jetzt zeichnet sich ab, dass sich der Einsatz gelohnt hat. Alle Entwicklerinnen und Entwickler arbeiten seit dem ersten Tag ganz selbstverständlich mit den neuen Lösungen, auch wenn das einige Umstellungen mit sich gebracht hat. Daran hat neben dem umfassenden Change-Management, den Schulungen und der Dokumentation sicher auch der aktuelle Hypercare-Support seinen Anteil: Niemand wird alleingelassen, Hilfe ist immer verfügbar.
Mit der Einführung von Siemens NX und Teamcenter sowie von SAP S/4HANA hat Bomag die Grundlage geschaffen, vorhandene Daten optimal zu nutzen. Nächste Schritte sollen nun folgen. Dazu gehört unter anderem, den Aufbau von digitalen Zwillingen für die Baumaschinen voranzutreiben. Auf dem Weg zu einer gesamtheitlichen Digitalisierung sollen die erfassten Daten auch in anderen Fachbereichen zum Einsatz kommen, um so noch flexibler auf die Anforderungen der Kunden reagieren zu können. Und schließlich möchte der Maschinenbauer die Erfahrungen, die im Laufe des Projekts zum agilen Vorgehen gesammelt wurden, im gesamten Unternehmen ausrollen.
Der Autor Michael Schwengers ist Fachredakteur in Köln.
Lesen Sie auch: Nvidia-Ada: Mehr Leistung für Ihre Produktivitätssteigerung